구리 인듐 (디)셀레나이드 ( CIS )는 구리, 인듐, 셀레늄으로 구성된 반도체 소재입니다. CIS는 일반적으로 저렴한 소다석회 유리 기판의 박막층으로 생산되는 황동석 구조를 사용하는 태양전지에 대한 더 나은 재료 선택 중 하나입니다. CIS, CIGS 및 CIGSS 합금 반도체의 중요한 장점은 최고 효율 범위를 포함하여 에너지 격차가 상당히 크다는 점입니다. [1] CIS 생산 방식에는 주요 생산 방식으로 CVD(Chemical Vapor Deposition)와 스퍼터링(Sputtering) [2] 이 있다. 현재 가장 효율적인 박막 CIS 태양전지판 효율은 17.7%이다. [삼]
CIS 반도체는 태양전지 업계의 과학자들이 자주 연구하고 살펴보고 있습니다. CIS 셀을 만드는 데 걸리는 매우 어려운 가공 방법으로 인해 이러한 셀을 대량 생산하기 어렵고 비용이 많이 듭니다. 이 물질을 탐구하는 이유는 Si보다 더 효율적인 태양전지를 만들 수 있기 때문이다. 갈륨은 종종 CIGS라고 하는 CIS에 추가됩니다. CIS에 소량의 갈륨을 추가하면 밴드갭이 일반 1.0전자볼트(eV)에서 1.7eV로 증가하여 전압이 향상되고 이에 따라 장치 효율도 향상됩니다. [4] 폐기물은 매우 가치가 높기 때문에 모든 광전지 재료의 주요 관심사 중 하나입니다. 이 프로젝트 내에서 폐기물 관리 및 가능한 재활용 프로세스를 탐구합니다.
내용물
태양광 생산 개요
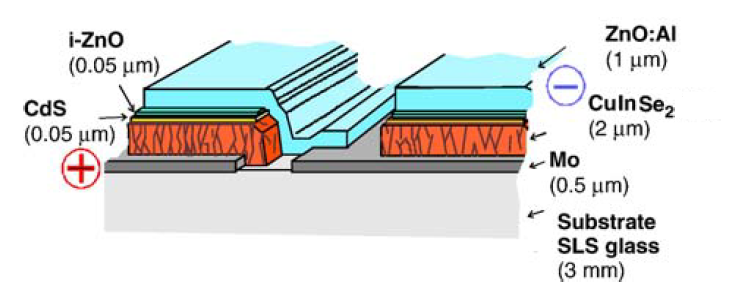
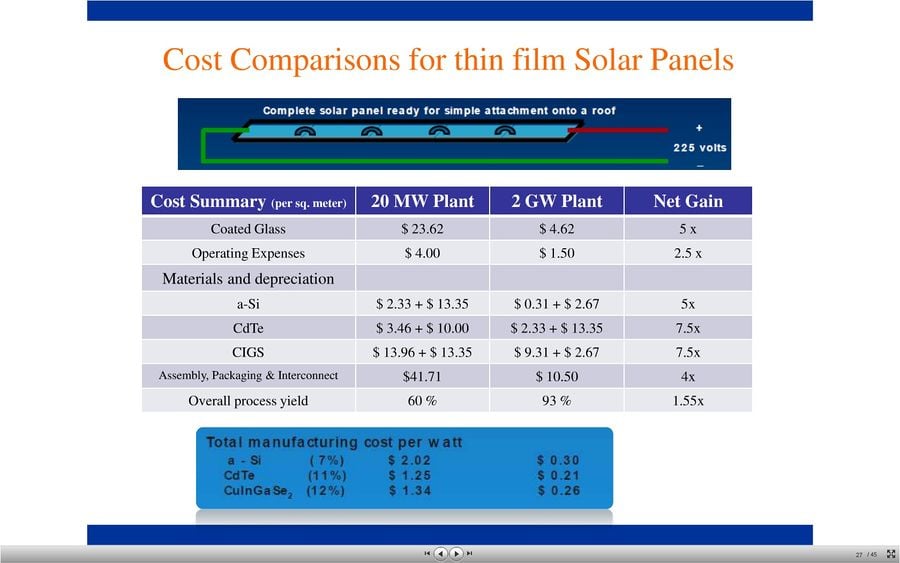
박막 태양광 모듈 생산은 현재 시장 점유율 1위인 결정질 실리콘(c-Si) 태양광 모듈과의 경쟁에서 가장 유망한 후보 중 하나입니다. 박막 재료 중에서 CIS와 그 합금은 현재 multi-c-Si 생산과 동등한 충분히 높은 효율(품질) 수준으로 제조되는 유일한 PV 재료입니다. [5] 박막의 중요한 이점은 향상된 처리량이며, c-Si와 비교할 때 넓은 면적의 증착으로 인해 발생합니다. 실험실에서 생산되는 것과 같은 효율성을 지닌 CIS 모듈은 아직 대면적 , 대규모 생산에서는 효과적으로 구현되지 못하고 있다. [5] CIS 및 그 합금 생산에는 진공 기반의 물리 기상 증착 및 화학 기상 증착 기술이 포함됩니다. 진공 기반 기술을 사용한 생산은 다단계 성장 공정으로 인해 최고 효율의 CIS 셀을 생산했습니다. [8] 비진공 기술에는 전착(전기 도금) 및 여러 입자 기반 기술이 포함됩니다.
기판
박막 태양전지 장치는 기판 또는 슈퍼스트레이트 구성으로 구성됩니다. 슈퍼스트레이트 구성은 기판이 투명하고(예: 유리의 경우) 기판의 전도성 산화물 코팅에 의해 접촉이 이루어지는 경우입니다. 기판 구성의 경우 기판은 금속이거나 접점 역할을 하기 위해 금속 코팅이 적용된 유리/폴리머로 구성됩니다. 기판은 장치의 수동 구성 요소이며 장치 제조 중에 기계적으로 안정적이고 불활성이어야 합니다. 유연한 기판, 스테인리스 스틸 포일/폴리머 필름은 롤투롤 증착에 적합하여 컴팩트한 증착 시스템 설계와 장치 취급의 유연성을 가능하게 합니다. 전기 전도성 기판을 사용하면 전면 및 후면 전도 셀을 제작할 수 있으며, 절연 기판을 사용하면 모듈용 단일체로 상호 연결된 셀을 제작할 수 있습니다 . [10] 동시 증발과 마찬가지로 고온은 증착 공정의 일부이므로 고온 유리나 세라믹과 같은 값비싸고 견고한 기판이 필요할 수 있습니다. 현재 CIS 제조에는 슈퍼스트레이트와 기판 장치 구조가 모두 포함됩니다. 금속박, 소다석회 유리 등. CIS/CIGS 전지 생산에 가장 일반적으로 사용되는 기판은 일반적인 두께가 3mm인 소다석회 유리입니다. [11] 스퍼터링을 사용하여 기판을 코팅한 다음 PVD 시스템을 사용하고 공동 증발을 통해 CIS 셀을 마무리할 수 있습니다.
투명 전도성 산화물(TCO)
일반적으로 투명 전도성 산화물은 가시 스펙트럼에서 우수한 전기 전도성과 높은 투명성을 갖는 n형 축퇴 반도체입니다. 장치에 대한 낮은 저항 접촉과 대부분의 입사광이 흡수층으로 전달되는 것이 보장됩니다. TCO 의 전도도는 캐리어 농도와 이동도에 따라 달라집니다. 이러한 광전자적 특성 외에도 TCO의 기계적, 열적, 화학적, 플라즈마 노출 안정성과 수동성이 중요한 고려 사항입니다. 연구에 따르면 ZnO 기반 TCO만이 H 함유 플라즈마를 견딜 수 있으며 최대 800K까지 안정적이라는 사실이 밝혀졌습니다. 따라서 ZnO 기반 재료는 태양광 기술에 점점 더 많이 사용되고 있습니다. 이중층을 형성함으로써 두 TCO의 서로 다른 특성을 활용하는 것이 가능합니다. 고효율 CIGS 및 CdTe 장치는 일반적으로 저저항 접촉 및 측면 전류 수집을 위한 전도성이 높은 층과 훨씬 더 얇은 고저항성 층(CIS/CIGS 그룹에서는 버퍼층이라고 함)으로 구성된 이중층 구조로 제조됩니다. 창 레이어의 핀홀을 통한 순방향 전류를 최소화하는 데 적합한 재료입니다. 50nm 두께의 저항성 SnO2, In2O3, ZnO 또는 Zn2SnO4 층을 통합함으로써 CdS 층 두께를 20nm 미만으로 줄일 수 있습니다. 더 부드러운 고저항층의 존재는 화학조 증착 중에 큰 입자를 제공함으로써 CdS 필름 형태를 향상시킵니다. 이중층 ZnO는 CIS 태양전지의 기판 구성을 위해 전면에 사용됩니다. 예를 들어, Wurth CIS 태양 전지 그림에는 CdS 및 ZnO 층이 모두 표시되어 있으며 생산에 사용되는 현재 두께가 제공됩니다.
창 레이어
이종접합에서 윈도우층의 주요 기능은 흡수층과의 접합을 형성하면서 접합 영역과 흡수층에 최대량의 광을 허용하는 것입니다. 창층에서는 광전류 생성이 발생하지 않습니다. 저항 손실을 최소화하면서 높은 광학 처리량을 얻으려면 창 레이어의 밴드갭이 가능한 한 높고, 낮은 직렬 저항을 유지하기 위해 최대한 얇아야 합니다. 최적의 소수 캐리어 전송을 위해서는 이종 접합에서 전도대의 잠재적인 '스파이크'를 최소화하는 것도 중요합니다. 접합부에서의 격자 불일치(및 그에 따른 효과)는 에피택시 또는 고도로 배향된 층을 고려할 때 중요합니다. [13] CIS/CIGS 태양전지는 일반적으로 전착(ED) 기술로 증착되는 CdS 창 층을 사용합니다. 이는 물리적 기상 증착(PVD) 기술로 증착한 것과 비교하여 우수한 장치 성능을 제공합니다. 이는 부분적 으로 화학 공정 중 CIGS와 CdS 사이 의 계면 화학이 향상되었기 때문입니다. 화학 용액은 CIS 필름 표면에서 자연 산화물을 제거하고 Cd가 CIS 필름의 Cu가 부족한 표면층으로 확산되도록 합니다. 또한 ED 증착은 10 nm의 필름 두께에서도 거친 다결정 CIS 표면의 우수한 표면 커버리지를 제공하기 때문에 더 얇은 CdS 층을 사용하는 것이 가능합니다. 티오 우레아가 없는 화학조에 CIS 필름을 담근 후 CdS 필름을 PVD 증착한 경우 유사한 장치 성능이 보고되었습니다. 윈도우 레이어로서 CdS의 상대적으로 낮은 밴드갭은 청색 응답을 감소시키지만 더 얇은 CdS 필름을 사용하면 CdTe 및 CIS 장치 모두에서 그 효과가 완화됩니다. CIGS와 같은 I-III-VI 필름 기반 장치의 경우 Cd의 독성에 대한 우려와 재료 재활용 문제로 인해 CdS를 대체하기 위해 현재 조사 중인 여러 대체 창 레이어가 있습니다. [10]
흡수체(CIS)
황동광 재료(CIS/CISS/CIGS)는 광전지 응용 분야에 매우 바람직한 특성을 가지고 있습니다. 1 eV의 밴드갭을 갖는 CuInSe 2 는 광전지 응용 분야의 주요 후보임이 입증되었습니다. CuInSe 2 및 기타 황동석은 광범위한 음이온-양이온 비화학양론을 허용하는 것으로 보입니다 . II-VI 유사체와 달리 CuInSe 2는 단지 고유 결함 도입을 통해 낮은 저항 수준으로 n형 및 p형을 도핑할 수 있습니다. 다결정 CuInSe 2 의 가장 유리한 특징은 수많은 구조적 결함의 전기적으로 온화한 특성에 있으며 따라서 다결정 CuInSe 2 필름은 단결정 대응물만큼 우수한 전자 재료입니다. 이는 CuInSe 2 기반 태양전지를 불순물, 입자 크기 및 결정 결함에 덜 민감하게 만듭니다. 15.4%의 활성 영역 효율을 갖는 장치 [15] 는 CuInSe 2 로 제작되었습니다 . 밴드갭을 증가시켜 접합이 태양 스펙트럼과 일치하면 우수한 장치 성능이 달성됩니다. Voc의 결과적인 증가는 또한 다음과 같은 방법으로 제조 공정 및 장치 특성에 이점을 줍니다. (a) 모듈에 셀을 모놀리식 통합하기 위한 스크라이브 수를 줄입니다. (b) 상부 및 하부 전극 두께를 감소시키는 단계; (c) 최대 전력점에서 온도 계수를 낮추는 단계; (d) 빛의 강도 변동에 덜 민감하게 만듭니다. 장치의 효율성과 안정성이 매우 유망하더라도 이러한 장치의 대규모 생산에는 덜 유리한 몇 가지 요소가 있습니다. 증착 중 조성을 정밀하게 제어하려면 지능형 프로세스가 필요합니다. 비싸고 희귀한 금속 In을 사용하면 제조 비용이 추가됩니다. CIS는 불순물에 덜 민감하기 때문에 진공 기반 공정과 관련된 과도한 비용으로 인해 여러 가지 비진공 전구체 증착 방법을 선호하여 고진공 공정이 보류되었습니다. 그러나 비진공 공정 중 어느 것도 진공 기술을 통해 생산된 전지의 효율성을 따라잡을 수 없었습니다. 전착 방법에서는 염화 구리(II) 이수화물, 삼염화 인듐, 셀렌산 및 염산을 화학 물질로 사용하여 CIS 층을 생성합니다. 셀렌화는 일반적으로 전착 필름의 최종 조성을 조정하기 위해 PVD와 함께 수행됩니다. 전착 필름은 13.6%의 효율을 달성했습니다. 입자 기반 기술을 사용하여 치밀한 필름을 생성합니다.
뒤로 연락처
다결정 CIS 장치의 경우 후면 접점은 슈퍼스트레이트 및 기판 구성 모두에서 p형 반도체에 적용됩니다. CIS 태양전지의 기판 구성에서 Mo는 부식성이 높은 CIS 증착 조건에서 상대적으로 불활성인 특성 때문에 접촉 재료로 사용됩니다. Mo는 CIS 증착 중에 형성된 얇은 중간 MoSe 2 층 의 형성을 통해 오믹 접촉을 형성합니다 . CIS 장치를 위한 몇 가지 대체 접촉 재료도 연구되었습니다. 기판에 대한 Mo 필름의 접착력과 시트 저항률은 스퍼터링 증착 조건에 따라 크게 달라집니다. 일반적으로 낮은 공정 압력에서 스퍼터 증착된 Mo 막은 밀도가 높고 저항률과 압축 응력이 낮은 경향이 있습니다. Ar 공정 가스 압력이 증가함에 따라 필름 응력은 압축에서 인장으로 전환됩니다. 흥미롭게도 Mo는 Superstrate 구성에서 CIS에 저항 접촉을 형성하지 않습니다. 아마도 MoSe 2 가 없고 Pt 및 Ti 필름이 대신 사용되기 때문일 것입니다 . 스퍼터링은 후면 접점을 생성하는 가장 일반적인 방법입니다.
다단계 진공 처리
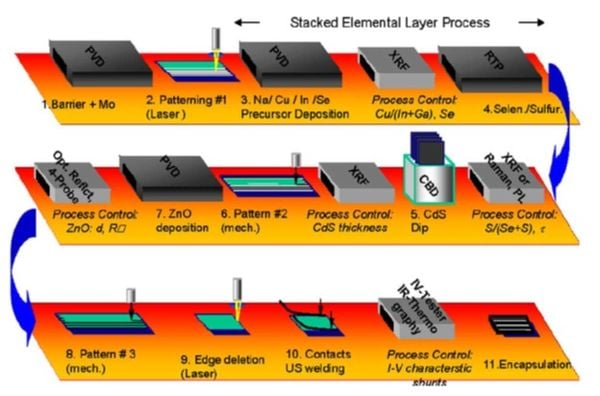
대량생산을 위한 CIS 태양전지 제조는 PVD 공증착 및 열생산 방식이 가장 일반적으로 이루어지고 있다. 공증착 외에도 CdS의 버퍼층은 일반적으로 화학욕 증착을 사용하여 적용되는 유일한 층입니다. 다만 전착법, 셀렌화법 등도 사용되나 주로 PVD법에 초점을 둘 예정이다. 그림 3에는 CIS 태양전지 제조와 관련된 단계를 보여주는 공정 흐름도가 나와 있습니다. 표 1은 증착 방법과 결과적인 장치 효율성 및 생산 공정에서 발생하는 폐기물 간의 비교를 제공합니다.
표 1: CIS의 증착 방법, 결과적인 효율성 및 공정 폐기물
PV 증착 기술 | 결과적인 광전지 효율(%) | 공정폐기물(%) |
---|---|---|
공동 증발 | 17.7 [3] (모듈) 15.4 [15] (셀) 11.7 [18] (모듈) 13.1 [19] (모듈) | < 20 [20] |
전착 | 13.6 [16] | < 10 [15] |
셀렌화 (연소/스핀코팅) | 11.0 [21] | < 40 [21] |
셀렌화 (입자 전구체) | 11.6 | < 30 [22] |
자본 및 소모품 요구 사항
자본 필수 재화는 다음과 같습니다.
- 진공 챔버
- 진공 펌프
- 수평 소스 증발기
- 전구체 층용 스퍼터링 시스템
- 레이저 에칭 기계
소모품:
기판 유리전기Mo, Cu, In, Se, Cd, Zn을 포함한 증착 원소.Thiourea의 화학조 소모품,
CIS 모듈 제조를 위한 주요 투입물
소비된 자원의 값은 표 2에 나와 있습니다. 알루미늄 프레임이 없는1m 2 CIS 모듈의 경우.
표 2: CIS 모듈 제조를 위한 입력
섭취 | 소모량 |
---|---|
유리 | 24,960g/m 2 [23] |
물 | 1250g/m 2 [23] |
에바 | 880g/m 2 [23] |
Mo+Cu+In+Se+ CdS+ZnO+CuSn | 70g/m 2 [23] |
총 전력 | 24.3kWh/m 2 [23] |
생산 폐기물 재활용
제조 과정에서 여러 증착 단계와 화학조를 거쳐 폐기물이 생성됩니다. 1kW 모듈 입력에 대해 방출된 슬래그, 필터 먼지 및 가스 먼지의 양은 슬래그 생산량이 각각 200g과 1.5g, 필터 먼지가 43g과 0.5g, 가스 먼지가 구리와 카드뮴에 대해 각각 4g과 0.05g이 생성됩니다. [24]
수명이 다한 태양광 모듈 재활용 개요
수명이 다한 PV 모듈 재활용에 중점을 둘 때 다음 사항을 고려하는 것이 중요합니다. 재활용을 위한 태양광 모듈 수집은 모듈의 분산으로 인해 잠재적인 문제가 됩니다. 그러나 재활용은 대규모 중앙 집중식 시설이 위치한 곳에서 훨씬 더 경제적으로 실현 가능합니다. 태양전지에 포함된 귀중한 물질의 총 농도는 극히 낮습니다. CIS 태양전지에 사용되는 박막 구성 요소 중 가장 비싼 인듐은 CIS 모듈 전체 예상 비용의 2.5~5%만을 차지합니다. 이러한 이유로 PV 모듈을 재료비만으로 재활용하는 것은 경제적으로 실행 가능하지 않을 것 같습니다. 그러한 공장에 대한 수입의 대부분은 재활용 회사가 모듈을 가져가는 데 비용을 지불하는 고객에게서 나올 가능성이 더 높습니다.
생산 과정에서 발생하는 폐기물 재활용을 살펴보면 몇 가지 주요 문제가 떠오릅니다. 생산된 각 PV 모듈당 폐기물의 양이 급격히 감소하고 있습니다. 이는 태양광 발전이 주류로 자리잡으면서 현재의 생산 방법이 보다 효율적으로 개선되고 새로운 고효율 생산 방법이 개발되고 있기 때문입니다. 약 1GW의 전력을 생산할 수 있는 200,000톤의 태양광 패널을 생산할 수 있는 공장을 건설한 첫 해 이후에는 연간 10,000톤의 재활용 가능한 폐기물이 발생할 것으로 예상됩니다. 고려해야 할 주요 문제는 이러한 모듈 처리에 사용되는 대부분의 폐기물을 사내에서 정제할 수 있다는 것입니다. 이는 폐기된 수명이 다한 모듈을 향해 PV 모듈을 재활용하는 데 중점을 두고 있습니다. 이러한 관점에서 생산이 시작된 지 20년이 지난 1GW PV 생산업체의 폐기물을 살펴보면 재활용 플랜트에서는 연간 대략 210,000톤의 폐기물이 발생할 것으로 예상할 수 있습니다. 이 규모의 PV 제조 공장은 아직 달성되지 않았으므로 이러한 값은 가정을 기반으로 한다는 점에 유의하는 것이 중요합니다.
생산 공정의 모든 단계에서 귀중한 재료가 전반적으로 부족하기 때문에 현재 가장 기대할 수 있는 것은 다운사이클링일 가능성이 높습니다. 이는 CIS 모듈에 사용되는 금속 가격이 지속적으로 상승할 것이라는 사실을 고려하지 않은 것입니다. PV 모듈에 사용되는 재료를 다시 재활용하는 데에는 재정적 이점이 거의 없습니다. 대신 재료 재활용이 일부 보조 재료로 사용될 가능성이 가장 높습니다. 태양광 재활용 기술의 경우 놀라운 속도로 혁신이 일어나고 있습니다. 이는 재활용 비용과 재료 자체의 비용이 계속해서 크게 변동한다는 것을 의미합니다. 마찬가지로 매립에 자재를 투입하는 비용도 지속적으로 상승합니다.
다운 사이클링과 직접 재활용의 경우 무엇보다도 비용과 이익을 살펴보는 것이 중요합니다. 다운 사이클링은 금속 순도가 PV 모듈에서 재사용되는 순도와 동일한 수준일 필요가 없기 때문에 재활용과 관련된 비용을 줄여줍니다. 위에서 언급한 바와 같이 재활용 PV 재료의 가장 유력한 고객은 유리용 실리카를 사용하는 제련소일 것입니다. 제련소는 또한 재활용 시설에서 재료 분리 단계를 제거할 수 있도록 금속을 더욱 정제할 수 있습니다. 직접 재활용의 장점은 순도가 높아 최종 재료의 이익이 증가한다는 것입니다. 또한 재활용 공장이 재활용 공정이 끝날 때 PV 재료를 공급하는 경우 제조업체가 재활용 공장을 지원하는 데 더 많은 인센티브가 있습니다.
폐반도체의 회수방법은 2가지가 있습니다. 첫 번째 경우는 재활용 공장이 폐기물 수거 또는 역소매를 통해 셀 밀도가 낮은 여러 장소에서 중고 반도체를 구입해야 한다는 것입니다. 두 번째 수거 사례는 폐기물을 직접 운송하는 방식으로 반도체 생산 공장과 재활용 공장 간의 상생 관계입니다. 이는 생산공장이 폐기물 처리를 무료로 받고, 재활용 공장이 더 높은 수익을 얻을 수 있다는 점에서 가장 유리한 경우이다. [25] 이러한 잠재적 책임의 비용은 정량화하기 어렵습니다. 한 가지 접근 방식은 여기에 오늘날의 유해 폐기물 처리 비용(미국의 평균 $800/ton)과 동일한 가치를 할당하는 것입니다. 이는 오늘날의 박막 태양전지의 W당 0.09~0.10달러에 해당하며, 이는 수집 및 재활용에 드는 전체 비용을 충당합니다. 미래 책임 회피를 가정하면 재활용 비용은 0이 됩니다. [25]
습식 기계 공정
일부 태양광 모듈에 포함된 위험 물질은 적절하게 폐기하지 않으면 해로울 수 있습니다. 이러한 일이 발생하지 않도록 하려면 적절한 수명 종료 후 재활용 및 폐기가 필요합니다. 이를 위해 우리는 (습식) 기계 공정을 사용하여 광전지 박막 모듈을 재활용하는 방법을 살펴보았습니다. 습식 공정을 사용하면 수명이 다한 모듈을 처음에는 손상되지 않은 캐리어 유리와 두 번째로 깨진 모듈로 재활용하는 기본 단계는 동일합니다. 이러한 단계에는 라미네이트 층 파괴, 유리 기판에서 반도체 분리, 반도체 재료 강화, 더 많은 박막 모듈 생산을 위한 재활용 반도체 재료 재사용이 포함됩니다. [26]
라미네이트 층의 파괴
모듈의 라미네이트 층 파괴는 PV 모듈(30cm x 30cm 및 10cm x 10cm 조각)을 용광로에 넣고 약 500˚C의 온도로 가열함으로써 시작됩니다. 이로 인해 반도체와 후면유리 사이의 층인 EVA(Ethylene Vinyl Acetate)층이 완전히 파괴되었습니다. 라미네이트의 실제 파괴는 모듈을 20mm 이하의 입자로 분쇄하여 수행됩니다. 입자는 마모가 정서적으로 작용할 만큼 충분히 작아야 합니다. 작고 균일한 조각을 얻으려면 CIS를 파쇄기, 회전 전단기 및 임팩트 핀 밀에 넣어야 합니다. [26]
반도체층 분리
반도체 층의 분리는 모듈이 파손되었는지 여부에 따라 두 가지 다른 공정으로 수행됩니다. 캐리어 유리가 손상되지 않은 모듈의 경우 이 공정에서는 진공 블라스팅이 필요합니다. 이는 공기압 대신 진공을 사용하는 특수 블래스팅 기술입니다. 이는 분진 배출을 최소화하고 분사 매체의 폐쇄 회로를 가능하게 합니다. 손상된 모듈의 경우 Atrittion이 사용됩니다. 분쇄된 물질을 용기에 넣고 교반하고 전단력을 가합니다. 전단력은 화학물질을 추가하지 않고도 모듈 레이어를 제거할 수 있습니다. [26]
주식 상장
반도체 물질의 농축은 부유선광에 의해 수행됩니다. 이를 통해 다양한 재료가 서로 분리됩니다. 이 단계에서는 일련의 다양한 부유물과 원심력을 사용하여 불순물을 걸러냅니다. [26] 이 절차의 장점은 공정이 더 안전하고 화학 물질을 거의 사용하지 않는다는 것입니다. 이 공정은 마찰력을 사용하여 다양한 재료를 분리합니다. 이는 분리 공정에 화학 물질이 사용되지 않음을 의미합니다. 위험한 화학물질을 사용하지 않으면 안전 관련 비용이 절감될 것으로 기대할 수 있습니다. 재료의 최종 사용에 따라 이 공정을 사용하여 추가 처리가 덜 필요할 수 있습니다. 이 공정의 유가물 수율은 35.26%에 불과했습니다. [26]
화학물질 분리 공정
PV 모듈의 층을 화학적으로 분리하는 과정을 위해서는 먼저 모듈 전처리가 이루어져야 한다. 이 전처리는 단순히 위에서 설명한 습식 공정과 유사하게 재료를 작은 크기로 분쇄하는 것입니다. 이는 노출된 표면적의 증가로 인해 반응 과정의 속도를 높이고 효율성을 증가시킵니다.
먼저 세포를 질산 기반 용해제로 처리합니다. 침출제는 구리, 인듐, 셀레늄 및 아연을 선택적으로 산화하고 용해시킵니다. SnO2 전도성 층은 유리 기판에 그대로 유지됩니다. 라미네이트의 EVA 플라스틱은 가수분해되어 침출액 상단으로 떠다니며 회수하여 폐기할 수 있습니다. EVA는 추가 처리가 필요하지 않으며 폐기할 수 있습니다.
Cu, Se 및 Cd를 제거하기 위해 여러 전극이 있는 여물통에서 전체 규모 공정이 수행됩니다. 이 여물통에서 Cu와 Se는 용액 입구에 가장 가까운 전극에 끌리고 Cd는 용액 출구에 가장 가까운 전극에 축적됩니다. 용해제가 분해되면 인듐, 아연 및 잔류 금속 산화물이 생성됩니다. 그런 다음 추가 용매 추출을 위해 정제소에 판매될 수 있습니다.
안전
산업 공정을 시작할 때 환경, 건강 및 안전 문제를 해결해야 합니다. 안전 및 수명 종료 분석은 프로젝트의 이 섹션에서 다루어질 것입니다. 이 프로젝트에 사용된 보고서에는 연방 및 캘리포니아 주 환경이 고려되었습니다.
우리가 살펴본 기계적 재활용 공정의 경우 PV 모듈의 분리는 주로 파쇄력과 전단력에 의해 수행됩니다. 이 과정이 환경적인 측면에서 가장 좋은 것 같았습니다. 이 프로세스로 인한 유일한 추가 안전 문제는 중장비가 있을 때마다 처리해야 하는 문제이므로 이 섹션에서는 설명하지 않습니다. 화학적 분리 공정의 경우 모듈을 전처리하기 위해 분쇄가 계속 수행되므로 중장비에 대한 우려 사항을 해결해야 합니다. 화학 공정을 위한 기계 이외에 질산은 화학 분리 공정에도 사용됩니다. 이 화학물질과 이 공정을 통해 생산되는 기타 부산물에 대한 안전 계획을 마련해야 합니다. 안전 친구는 공정마다 다르며 개발되는 모든 공장에 필요합니다.
특정 재생 프로세스를 거치는 CIS PV 재료는 연방 및 캘리포니아 주 규정에 따라 위험하지 않은 것으로 간주될 가능성이 높습니다. 수명이 다한 CIS PV 재료는 대부분의 경우 규제되지 않은 비유해 쓰레기입니다. 결함이 있는 CIS 플레이트는 연방 규정에서 면제될 가능성이 높으며 회수를 위해 사내 분리 및 전처리를 거칠 수도 있습니다. [28]
대부분의 CIS 모듈은 수명이 다해도 위험 물질로 분류되지 않으므로 이러한 물질을 운송하고 처리하는 것이 더 쉬워집니다. 유일한 문제는 잠재적으로 유해한 물질의 농도가 너무 낮기 때문에 비용이 많이 들고 번거로운 폐기를 피하기 위해 재활용할 이유가 거의 없다는 것입니다. CIS PV 모듈 재활용 공장의 경우 공장에서 가져온 모듈은 폐기물로 간주되지 않습니다. [28] 위에 나열된 정보로 인해 외부 재활용 공장에서 처리할 CIS 모듈은 유해 폐기물 규정에서 면제될 가능성이 높습니다. 이는 결함이 있는 모듈과 수명이 다한 모듈 모두에 해당됩니다. 이는 CIS 태양광 재활용 플랜트를 계획할 때 비용을 크게 줄일 수 있지만 CIS 모듈에 포함된 독성 또는 유해할 수 있는 화학 물질을 여전히 고려해야 합니다. CIS 모듈에는 잠재적 으로 유해한 물질이 포함되어 있습니다. 그러나 이러한 화학 물질은 소량입니다. 카드뮴은 이러한 물질 중 가장 유해합니다. [29] 카드뮴 사용이 더욱 제한됨에 따라 우리는 이 원소에 대한 설명과 문제를 포기하기로 결정했습니다. CIS 모듈과 관련된 기타 유해 물질로는 셀레늄, 몰리브덴 및 인듐이 있습니다. 재활용 공장을 시작할 때 계획해야 할 자재 중 일부는 다음과 같습니다. 이러한 물질의 농도는 대부분의 경우 안전이나 건강 관련 문제가 발생할 가능성이 미미할 정도입니다. 역물류 회사는 이미 수집, 통합 및 제조업체와 재활용업체로 운송을 담당하고 있습니다. [28] 이러한 모듈의 운송에 대한 안전 문제는 이미 인프라가 갖춰져 있고 재료가 위험하지 않은 것으로 간주될 가능성이 높기 때문에 작은 것으로 볼 수 있습니다.
MSDS
질산
구리(II) 염화물 이수화물 삼염화
인듐 셀렌산
염산
구리
인듐
셀레늄
카드뮴
황화물 산화
아연
몰리브덴 티오
우레아
자본 장비
1GW의 전력을 생산하기에 충분한 태양광 모듈을 생산할 수 있는 태양광 제조 공장이 연간 10,000톤의 폐기물과 함께 200,000톤의 태양광 모듈을 생산한다고 가정하면 필요한 장비를 찾을 수 있습니다. 이 주제에 대한 과거 보고와 실험을 통해 우리는 이 과정에서 발생하는 대부분의 폐기물이 사내에서 재활용될 수 있다는 것을 발견했습니다. 따라서 이 공장의 모든 모듈이 수명이 다할 때 재활용될 것이라고 가정하면 이 정도 규모의 공장은 건설되지 않았으며 앞으로도 그럴 가능성이 없다는 점을 염두에 두고 매년 약 200,000톤의 폐기물이 발생할 것으로 예상할 수 있습니다. 비교적 빨리 건설될 것입니다. 이를 통해 우리는 매일 공장에 들어가는 원자재가 약 550톤이 될 것으로 예상할 수 있었습니다. 이는 공장이 1년 365일 가동된다는 가정이다.
매일 600톤의 PV 재료를 처리할 수 있는 습식 기계 공정에 필요한 자본 장비
Crushing Mill – 유리 합판을 분쇄할 수 있는 분쇄기
산업용 용광로 - 용광로의 실제 크기는 가동 시간, 알 수 없는 PV 재료 처리 시간에 따라 변경됩니다(실험은 매우 작은 재료량에 대해서만 수행되었으므로 이 실험에서 숫자를 기준으로 값을 기준으로 하는 것은 비현실적입니다). , 재료 밀도는 대략 2650kg/m3입니다.
Shredder, Rotating Shear, Impact Pin Mill – 균일한 유리알갱이 생산 가능
진공 블래스터 – 진공 블래스터에 필요한 사양에 대해서는 알려진 바가 거의 없습니다.
부양 시스템 – 대형 회전 드럼과 다양한 재료에 대한 다양한 필터를 갖춘 다단계 부양 시스템
일일 600톤의 PV 재료를 처리할 수 있는 화학 분리 공정용 자본 장비
Crushing Mill – 유리 합판을 분쇄할 수 있는 분쇄기
혼합탱크 - PV재료와 질산을 담고 혼합할 수 있는 탱크
전기분해 시스템 – 금속을 제거할 수 있는 여러 개의 전극이 있는 여물통 같은 구성
진공 후드 - 화학적 분리 공정에서 유해한 가스를 제거할 수 있습니다.
나열된 장비 이외의 모든 건강 및 안전 장비는 OSHA 표준을 따릅니다.
- ↑ A. Rockett, RN Bhattacharya, V. Kapur, SH Wei, CU-Chalcopyrite Photovoltaics의 기본 연구 기회 , 1999년 4월, NREL/CP-520-29587
- ↑ Kemell, M., Ritala, M., & Leskelä, M. (2005). "CuInSe2 태양전지의 박막 증착 방법". 고체 및 재료 과학의 비판적 검토, 30(1), 1-1-31. Proquest 에서 검색함 .
- ↑다음으로 이동:3.0 3.1 미국 에너지부, 구리 인듐 디셀레나이드 - 광전지 재료로서 , 2002년 1월.
- ↑ 태양에 대한 사실 및 조언, Alchemie Limited Inc. ( http://www.solar-facts-and-advice.com/CIGS-solar-cell.html )
- ↑다음으로 이동:5.0 5.1 5.2 Bernhard Dimmler, Rolf Wächter, CIS 태양광 모듈의 제조 및 응용 , Thin Solid Films, Volume 515, Issue 15, 2007년 5월 31일, 페이지 5973-5978, ISSN 0040-6090, 10.1016/j.tsf.2006.12.150 .
- ↑ Zhang Xuan, Rajendiran Aravind Raj, Wu Yiming., CIGS 태양 전지: 비용이 어떻게 그리고 왜 하락합니까?
- ↑ Green, MA (2006), 박막 광전지 기술의 통합: 다가오는 10년의 기회 ., 광전지 발전: 연구 및 응용, 14: 383–392. 도이: 10.1002/pip.702
- ↑ Udai P. Singh 및 Surya P. Patra, 다결정질 박막 Cu(In,Ga)Se2 태양전지의 발전 , 국제 저널 오브 포토에너지, 2010년판, 기사 ID 468147, 19페이지 doi:10.1155/2010/468147
- ↑ AE Delahoy, JS Britt 및 ZJ Kiss, CIS Photovoltaic Technology , 1998년 10월, NREL/SR-520-25713
- ↑다음으로 이동:10.0 10.1 10.2 10.3 10.4 K. L. Chopra, PD Paulson 및 V. Dutta, 박막 태양전지: 개요 , Prog. 광전지: Res. 신청 2004년; 12:69–92 doi: 10.1002/pip.541
- ↑다음으로 이동:11.0 11.1 T.J Gillespie, CH Marshall, M Contreras, J Keane, 구리 인듐 디셀레나이드(CIS) 공정, 제어 및 제조 , 태양 에너지 재료 및 태양 전지, 59권, 1~2호, 1999년 9월, 27~34페이지, ISSN 0927-0248, 10.1016/S0927-0248(99)00028-8.
- ↑다음으로 이동:12.0 12.1 12.2 M.E Calixto, PJ Sebastian, RN Bhattacharya, Rommel Noufi, 전착으로 형성된 CIS 및 CIGS 박막의 구성 및 광전자 특성 , 태양 에너지 재료 및 태양 전지, 59권, 1999년 9월 1~2호, 75페이지 84, ISSN 0927-0248, 10.1016/S0927-0248(99)00033-1.
- ↑다음으로 이동:13.0 13.1 Franz H Karg, CIS 박막 태양광 모듈의 개발 및 제조 , 태양 에너지 재료 및 태양전지, 66권, 1-4호, 2001년 2월, 페이지 645-653, ISSN 0927-0248, 10.1016/S0927-0248( 00)00256-7.
- ↑ PJ Sebastian, ME Calixto, RN Bhattacharya, Rommel Noufi, 전착 전구체로 개발된 CIS 및 CIGS 기반 광전지 구조 , 태양 에너지 재료 및 태양 전지, 59권, 1~2호, 1999년 9월, 페이지 125-135, ISSN 0927- 0248, 10.1016/S0927-0248(99)00037-9.
- ↑다음으로 이동:15.0 15.1 15.2 Green MA, Emery K, King DL, Igari S, Warta W. 태양전지 효율표(버전 21) . 태양광발전 분야의 발전: 연구 및 응용 2003; 11:39~45
- ↑다음으로 이동:16.0 16.1 크리스 에버스파처, 크리스 프레드릭, 카렌 폴스, 잭 세라; 비진공, 입자 기반 기술을 사용하여 제조된 박막 CIS 합금 PV 재료 , Thin Solid Films, Volume 387, Issues 1-2, 2001년 5월 29일, 페이지 18-22, ISSN 0040-6090, 0.1016/S0040-6090( 00)01729-6.
- ↑ Jörg Palm, Volker Probst, Franz H. Karg, 2세대 CIS 태양광 모듈 , Solar Energy, 77권, 6호, 2004년 12월, 페이지 757-765, ISSN 0038-092X, 10.1016/j.solener.2004.05.011.
- ↑ 스트랜드, T.; 크로포스키, B.; 한센, R.; Willett, D.;, Siemens 태양광 CIS 태양광 모듈 및 시스템 성능 at the National Renewable Energy Laboratory , Photovoltaic Specialists Conference, 1996., Conference Record of the Twenty Fifth IEEE, vol., no., pp.965-968, 13- 1996년 5월 17일 doi: 10.1109/PVSC.1996.564290
- ↑ M. Powalla, G. Voorwinden, D. Harriskos, P. Jackson, R. Kniese, 공동 증발 공정으로 제작된 고효율 CIS 태양전지 및 모듈 , Thin Solid Films, 517권, 7호, 2009년 2월 2일, 페이지 2111-2114, ISSN 0040-6090, 10.1016/j.tsf.2008.10.126.
- ↑ Green MA, Emery K, King DL, Igari S, Warta W. 태양전지 효율표(버전 36) . 태양광 발전의 진전: 연구 및 응용 2010,18:346–352
- ↑다음으로 이동:21.0 21.1 Paifeng Luo, Ruzhong Zuo, Litao Chen, 연소 방법 및 비진공 스핀 코팅 공정에 의한 CuInSe 2 필름 의 제조 , 태양 에너지 재료 및 태양 전지, 94(2010) 페이지 1146–1151
- ↑ M. Kaelin, D. Rudmann, F. Kurdesau, T. Meyer, H. Zogg, AN Tiwari, 셀렌화 나노입자 전구체의 CIS 및 CIGS 층 , Thin Solid Films, Volumes 431-432, 2003년 5월 1일, 페이지 58-62 , ISSN 0040-6090, 10.1016/S0040-6090(03)00194-9
- ↑다음으로 이동:23.0 23.1 23.2 23.3 23.4 Marco Raugei, Silvia Bargigli, Sergio Ulgiati, 고급 광전지 모듈의 수명 주기 평가 및 에너지 투자 회수 시간: CdTe 및 CIS와 폴리-Si 비교 , Energy, 32권, 8호, 2007년 8월, 1310페이지 -1318, ISSN 0360-5442, 10.1016/j.energy.2006.10.003.
- ↑ 썸, W.; 핀케, A.; 노이마이어, B.; 벡, B.; 케트럽, A.; 스타인버거, H.; Moskowitz, PD;, CIS 모듈 생산, 사용 및 폐기의 환경 및 건강 측면 , 태양광 에너지 변환, 1994., 1994 IEEE First World Conference on, vol.1, no., pp.262-265 vol.1, 5 -1994년 12월 9일, doi: 10.1109/WCPEC.1994.519858
- ↑다음으로 이동:25.0 25.1 25.2 25.3 25.4 Vasilis M. Fthenakis, 수명 종료 관리 및 PV 모듈 재활용 , 에너지 정책, 28권, 14호, 2000년 11월, 페이지 1051-1058, ISSN 0301-4215, 10.1016/S0301-4215( 00)00091-4.
- ↑다음으로 이동:26.0 26.1 26.2 26.3 26.4 Wolfgang Berger, Franz-Georg Simon, Karin Weimann, Erik A. Alsema, 박막 광전지 모듈의 재활용을 위한 새로운 접근 방식, 자원, 보존 및 재활용, 54권, 10호, 2010년 8월, 711페이지 -718, ISSN 0921-3449, 10.1016/j.resconrec.2009.12.001.
- ↑ 구즈너, RE; 드링크드, WF; 롱, 미주리; Byrd, CM;, 박막 PV 재료를 재활용하는 프로세스 , Photovoltaic Specialists Conference, 1997., 제26차 IEEE 회의 기록, vol., no., pp.1161-1163, 1997년 9월 29일~10월 3일 doi: 10.1109/PVSC.1997.654295
- ↑다음으로 이동:28.0 28.1 28.2 28.3 C. Eberspacher, VM Fthenakis* 및 PD Moskowitz; CuInSe 2 광전지 상용화와 관련된 환경, 건강 및 안전 문제 , 1996년 7월, Brookhaven 국립 연구소, BNL-63334.
- ↑ PD Fthenakis, VM Moskowitz, 태양광 발전: 환경, 건강 및 안전 문제 및 관점 , 태양광 발전 발전(2000), Vol 8; 1부, 27-38페이지
- ↑ 어머, J.; 게이, R.; 피어, D.; Tarrant, D.;, CuInSe2 박막 광전지 기술 규모 확대의 과제 및 진행 상황 , Journal of Vacuum Science & Technology A: Vacuum, Surfaces, and Films, vol.11, no.4, pp.1888-1895, Jul 1993년 도이: 10.1116/1.578518
- ↑ T. 토도로프, E. 코르돈시요, JF 산체스-로요, J. 카르다, 그리고 P. Escribano, 저비용 방법으로 증착된 광전지 응용을 위한 CuInS 2 필름 , 재료 화학 2006 18 (13), 3145-3150