Copper indium (di)selenide (CIS) is a semiconductor material composed of copper, indium, and selenium. CIS is one of the better material choices for solar cells using a chalcopyrite-structured, which generally are produced by from thin-film layers on inexpensive soda-lime glass substrates. The significant advantages of CIS, CIGS and CIGSS alloyed semiconductors are the significantly large ranges of energy-gaps they span, including the highest efficiency range.[1] CIS production methods include Chemical Vapor Deposition (CVD) and Sputtering[2] as the primary methods of production. Currently the most efficient thin film CIS solar panel has an efficiency of 17.7%.[3]
CIS semiconductors are studied and looked at often by scientists in the solar cell industry. The extremely difficult processing method it takes to make CIS cells makes these cells hard to mass produce and very costly. The reason for exploring this material is that it could make a more efficient solar cell than just Si. Gallium is often added to CIS which is refered as CIGS. Adding small amounts of galium to CIS boosts its bandgap from its normal 1.0 electron-volts(eV) to 1.7eV, which improves the voltage and therefor the efficiency of the device.[4] Waste is one of the major concerns with all photovoltaic materials because they are so valuable. Within this project waste management and possible recycling processes will be explored.
Overview of Photovoltaic Production[edit | edit source]
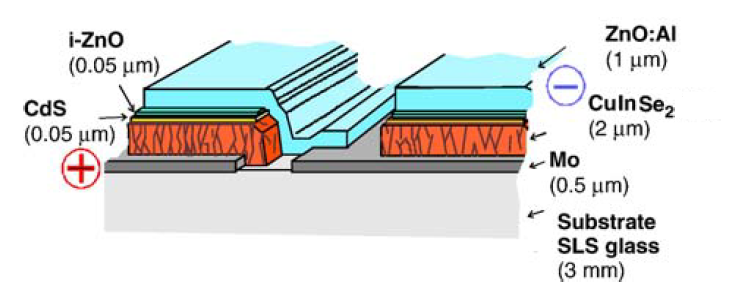
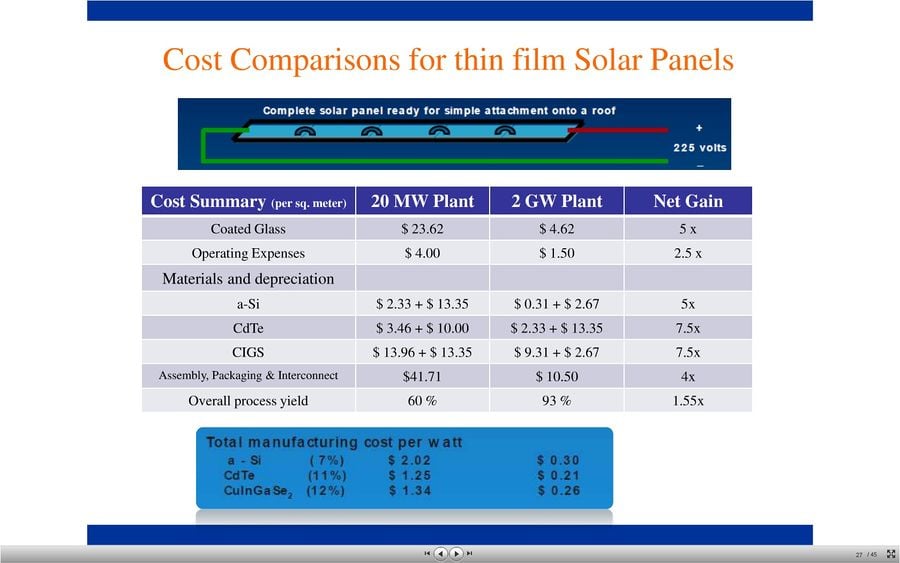
Production of thin film solar modules are one of the most promising candidates for competition against the current leading market share holder, crystalline silicon (c-Si) solar modules. Of the thin film materials, CIS and its alloys are the only PV materials which are currently manufactured on a high enough efficiency (quality) level on par with multi-c-Si production.[5]Significant advantages for thin films, are the enhanced throughput, and when compared to c-Si due to the large area depositions.[7] CIS modules with efficiencies as produced in laboratories are yet to be effectively realized in the large area and large-scale production.[5]Production for CIS and its alloys include the vacuum based techniques of Physical Vapor Deposition and Chemical Vapor Deposition. Production using vacuum-based techniques have yielded the highest efficiency CIS cells due to multi-stage growth processes.[8] Non-vacuum techniques include electro-deposition(electro-plating) and several particle-based techniques.
Substrate
Thin-film solar cells devices are configured in either substrate or a superstrate configuration. A superstrate configuration is when the the substrate is transparent (such as in the case of glass) and a contact is made by a conducting oxide coating on the substrate. With the substrate configuration, the substrate is metallic or comprised of a glass/polymer which has a metallic coating applied in order to act as a contact. Substrate is a passive component in the device and is required to be mechanically stable and inert during the device fabrication. Flexible substrates, stainless steel foils/polymer films, are suitable for roll-to-roll deposition enabling a compact deposition system design as well as flexibility in device handling.[9] Electrically conductive substrate enables the fabrication of front and rear-side conduction cells, whereas insulating substrate enables fabrication of monolithically interconnected cells for modules.[10] As with co-evaporation, high temperatures are part of the deposition process, which means it may require expensive and rigid substrates such as high-temperature glass or ceramics. Presently, CIS fabrication includes both superstrate and substrate device structures. Such as metallic foils and soda-lime glass. The most commonly employed substrate for the production of CIS/CIGS cells is soda-lime glass with a typical thickness of 3 millimeters.[11] Sputtering can be used to coat the substrate and then PVD systems would be used and with co-evaporation finish the CIS cell.
Transparent Conducting Oxide(TCO)
Transparent conducting oxides in general are n-type degenerate semiconductors with good electrical conductivity and high transparency in the visible spectrum. A low-resistance contact to the device and transmission of most of the incident light to the absorber layer is ensured.[10]The conductivity of a TCO depends on the carrier concentration and mobility. Besides these optoelectronic properties, the mechanical, thermal, chemical, and plasma-exposure stability and passivity of TCOs are important considerations. Studies have shown that only ZnO-based TCOs can withstand H-bearing plasma and are also stable up to 800K.[12] Therefore, ZnO-based materials are being increasingly used in solar technologies. It is possible to take advantage of differing properties of two TCOs by forming a bilayer. High-efficiency CIGS and CdTe devices are generally fabricated with such bilayer structures, consisting of a highly conducting layer for low-resistance contact and lateral current collection and a much thinner high-resistivity layer (called buffer layer by CIS/CIGS groups) of a suitable material, to minimize forward current through pinholes in the window layer. By incorporating a 50-nm-thick resistive SnO2, In2O3, ZnO, or Zn2SnO4 layer, the CdS layer thickness can be reduced to <20 nm. The presence of the smoother high-resistive layer also improves the CdS film morphology by providing large grains during chemical bath deposition.[10]Bilayer ZnO is used in CIS solar cells on the front side for substrate configuration. As an example, in the Wurth CIS solar cell figure, both the CdS and ZnO layers are shown and given in the current thicknesses they are employed at for production.
Window Layer
The primary function of a window layer in a heterojunction is to form a junction with the absorber layer while admitting a maximum amount of light to the junction region and absorber layer; no photocurrent generation occurs in the window layer. For high optical throughput with minimal resistive loss the bandgap of the window layer should be as high as possible and as thin as possible to maintain low series resistance. It is also important that any potential 'spike' in the conduction band at the heterojuction be minimized for optimal minority carrier transport. Lattice mismatch (and consequent effects) at the junction is important for consideration for epitaxial or highly oriented layers..[13] The CIS/CIGS solar cells typically use a CdS window layer, which is deposited by a electro-deposition (ED) technique, which provides a superior device performance compared with that deposited by a physical vapour deposition (PVD) technique.[14][12]This is partly due to the improvement in the interface chemistry between CIGS and CdS during the chemical process. The chemical bath removes the natural oxides from the CIS film surface and also allows Cd to diffuse into the Cu-poor surface layer of the CIS films. In addition, it is possible to use thinner layers of CdS because ED deposition provides good surface coverage of the rough polycrystalline CIS surface, even at a film thickness of 10 nm.[12]Similar device performance has been reported when the CdS films are PVD deposited after CIS films dipped in the chemical bath without thiourea. The relatively low bandgap of CdS as a window layer reduces blue response, but the effect is mitigated in both CdTe and CIS devices by utilizing thinner CdS films. For devices based on I–III–VI films such as CIGS, there are several alternative window layers currently being investigated to replace CdS because of the concern about the toxicty of Cd, and the issues with recycling the material.[10]
Absorber (CIS)
Chalcopyrite materials (CIS/CISS/CIGS) have some very desirable properties for photovoltaic application. CuInSe2, which has a bandgap of 1 eV, has proved to be a leading candidate for photovoltaic applications.[11]CuInSe2 and other chalcopyrites appear to tolerate wide range of anion-to-cation off-stoichiometry. Unlike the II–VI analogue, CuInSe2 can be doped n-and p-type to a low-resistivity level merely via introduction of native defects. The most benevolent feature of polycrystalline CuInSe2 lies in the electrically benign nature of its numerous structural defects and hence polycrystalline CuInSe2 films are as good an electronic material as its single-crystal counterpart. This makes CuInSe2 based solar cells less sensitive to the impurities, grain size and crystalline defects. Devices with active area efficiency of 15.4%[15] have been fabricated from CuInSe2. Superior device performance is achieved when the junction is matched to the solar spectrum by increasing the bandgap. The resultant increase in Voc also benefits to the manufacturing process and device properties by: (a) reducing the number of scribes for the monolithic integration of the cells into module; (b) reducing the top and bottom electrode thickness; (c) lowering the temperature coefficient at maximum power point; and (d) making it less sensitive to light intensity fluctuations. Even though the efficiency and stability of the device are very promising, there are several factors that are less favorable for large-scale production of such devices. Intelligent processes are required for precise control of the composition during deposition. The use of a expensive and rare metal In adds to the cost of manufacturing. As CIS is less sensitive to impurities, high-vacuum processes have been put on the shelf in favor of several non-vacuum precursor deposition methods due to excessive costs associated with the vacuum-based processes. However, none of the non-vacuum processes have been able to match the cells produced through vacuum techniques in efficiency. Methods of electro-deposition use Copper (II) Chloride Dihydrate, Indium Trichloride, Selenious acid and Hydrochloric acid as the chemicals to produce the CIS layer. Selenization is generally to follow along with PVD to adjust final compositions for electro-deposited films. Electro-deposited films have achieved efficiencies of 13.6%.[16] Using particle based techniques, producing a dense film.
Back Contact
For poly-crystalline CIS devices, the back contact is applied to the p-type semiconductor in both superstrate and substrate configurations. In the substrate configuration of CIS solar cells, Mo is used as the contacting material because of its relatively inert nature during the highly corrosive CIS deposition conditions. Mo forms an ohmic contact via the formation of a thin intermediate MoSe2 layer formed during the CIS deposition.[13][10]Several alternative contact materials are also investigated for CIS devices. The adhesion of Mo films to the substrate and the sheet resistivity is highly dependent on the sputter deposition conditions. In general the Mo films sputter-deposited at low process pressure tend to be dense, having low resistivity and compressive stress. As the Ar process gas pressure increases, the film stress switches from being compressive to tensile. Interestingly, Mo does not form an ohmic contact to CIS in the superstrate configuration, probably because of the absence of MoSe2 and Pt and Ti films are used instead. Sputtering is the most common method to produce the back contact.
Multi-Stage Vacuum Processing
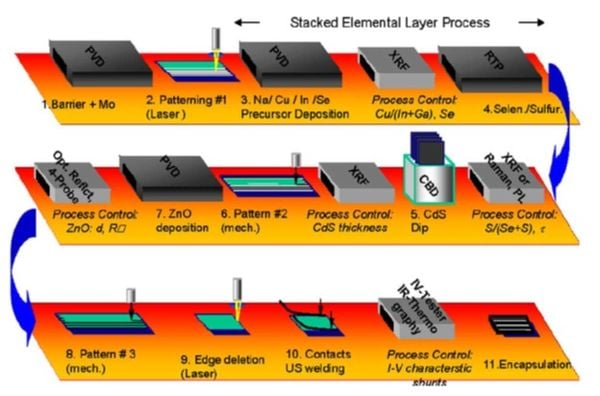
The manufacturing of the CIS photovoltaic cells for high-production is most commonly done by PVD co-deposition and thermal production method. Besides the co-deposition, the buffer layer of CdS is generally the only layer which is applied using a chemical bath deposition. However, methods of electro-deposition and selenization are used as well, but the focus will be on the primary method of PVD. Shown in figure 3, a process flow diagram is presented which shows the steps involved in the manufacture of the CIS solar cells. Table 1, provides a comparison between deposition methods and the resulting device efficiency and waste from the production process.
Table 1: Deposition Methods of CIS, Resulting Efficiency and Process Waste
Technique of PV Deposition | Resulting Photovoltaic Efficiency (%) | Process Waste(%) |
---|---|---|
Co-evaporation | 17.7[3](module) 15.4[15](cell) 11.7[18](module) 13.1[19](module) |
< 20[20] |
Electro-deposition | 13.6[16] | < 10[15] |
Selenization (Combustion/Spin-coating) |
11.0[21] | < 40[21] |
Selenization (Particle Precursor) |
11.6 | < 30[22] |
Capital and Consumables Requirements
Capital required goods include:
- Vacuum Chamber
- Vacuum Pumps
- Horizontal Source Evaporators
- Sputtering system for Precursor layers
- Laser Etching machinery
Consumables:
- Substrate Glass
- Electricity
- Deposition elements including Mo, Cu, In, Se, Cd, Zn.
- Chemical Bath consumables of Thiourea,
Main Inputs for CIS Module Manufacturing
Values for consumed resources are given in table 2; for a 1 m2 CIS module without the aluminum frame.
Table 2: Inputs for CIS Module Manufacturing
Intake | Amount Consumed |
---|---|
Glass | 24,960 g/m2[23] |
Water | 1250 g/m2[23] |
EVA | 880 g/m2[23] |
Mo+Cu+In+Se+ CdS+ZnO+CuSn |
70 g/m2[23] |
Total Electricity | 24.3 kWh/m2[23] |
Production Waste Recycling
During manufacturing, waste is produced through the multiple deposition steps and chemical bath. The amount of released slag, filter dust and gas dust for a 1 kW module input results in the slag production of 200 and 1.5 grams, filter dust of 43 and 0.5 grams and gas dust of 4 and 0.05 grams for copper and cadmium, respectively.[24]
Overview of End-of-Life Photovoltaic Module Recycling[edit | edit source]


When focusing on end of life PV module recycling it is important to take into account the following. Collection of photovoltaic modules for recycling is a potential problem due to dispersion of the modules. However recycling becomes much more economically feasible where large centralized installations are located. The total concentrations of valuable materials in solar cells are extremely low. Indium, the most costly of the thin-film constituents which is used in CIS solar cells, accounts only for 2.5–5% of the total projected cost of a CIS module.[25] For these reasons it does not seem like it will be economically viable to recycle PV modules for material cost alone. It will be more likely that most of the income for such a plant will be by customers paying for the recycling company to take the modules from them.
When looking at the recycling of waste material from the production process a few key problems come to mind. The amount of waste material per each PV module produced is decreasing drastically. This is because as solar power becomes more main stream current productions methods are being refined to become more efficient and new high efficiency production methods are being developed. It is expected that after the first year of production of a plant capable of producing 200,000 tons of solar panels capable of producing roughly 1 GW electricity would produce 10,000 tons of recyclable waste material a year.[25]The main problem to consider is that most waste material for the processing of these modules can be refined in house. This puts most of the focus for recycling PV modules towards decommissioned end of life modules. Looking at waste material from this stand point for a 1 GW PV producer twenty years after production is started a recycling plant could expect roughly 210,000 tons of waste material annually.[25]As a PV manufacturing plant of this size has not yet been achieved it is important to note that these values are based off assumptions.
The overall lack of valuable material at any stage of the production process makes it likely that currently the best possible thing to hope for is down-cycling. This is not taking into account the fact the price of metals used in the CIS modules will continue to rise. There are almost no financial advantages in recycling the materials to be used in PV modules again. Instead it is most likely that materials recycling will be used as some secondary material. In the case of photovoltaic recycling technology innovations are occurring at an astounding rate. This means that the cost of recycling and the cost of the material itself will continue to fluctuate greatly. On a similar note the cost of putting materials in land fill constantly rises.
In the case of down cycling vs. straight recycling it is important to look at cost vs. profit among other things. Down cycling would decrease the cost associated with recycling because metal purities would not need to be at the same level compared to those being reused in PV modules. As listed above the most probable customer for the recycled PV materials would be smelters using the silica for glass. The smelter would also be able to refine the metals further which would allow the recycling facility to remove any material separation steps. The advantages of straight recycling are increased profit of the final materials, due to the higher purity. There is also more incentive for the manufacturer to support the recycling plant if the recycling plant supplies them with PV materials at the end of the recycling process.
There are two possible collection methods for the out of use semiconductors. The first case is that the recycling plant has to acquire used semiconductors from multiple places in low cell densities by mean of waste collection or by mean of reverse-retail. The second case of collection is a mutual beneficial relationship between the semiconductor production plant and the recycling plant by mean of direct shipping of waste materials. This is the most beneficial case because the production plant recieves free waste disposal and the recycling plant can achieve a higher profit method.[25]The cost of this potential liability is difficult to be quantified; one approach is to assign to it a value equal to today's cost of hazardous waste disposal, which in the US is an average of $800/ton. This corresponds to $0.09–0.10/W for today's thin-film solar cells, which covers the entire cost of collection and recycling. Under this assumption of avoided future liability, the cost of recycling is zero.[25]
Wet Mechanical Process[edit | edit source]
Hazardous Materials in some Photovoltaic modules may become harmful if not disposed of properly. To stop this from happening proper end of life recycling and disposal is necessary. For this we have looked at recycling photovoltaic thin film modules using (wet-) mechanical processes. Using the wet process the primary steps for recycling end-of-life modules with firstly intact carrier glass and secondly broken modules are the same. These steps include destruction of the laminate layer, separation of the semiconductor from the glass substrate, enrichment of the semiconductor material, and re-use of the recycled semiconductor materials for the production of more thin film modules.[26]
Destruction of the laminate layer
The destruction of the laminate layer of the module is started by placing PV modules (pieces of 30cm x 30cm and 10cm x 10cm) in a furnace and heating them to temperatures of approximately 500 ˚C. This completely destroyed the EVA (Ethylene Vinyl Acetate)-layer which was the layer between the semiconductors and the back glass. The actual destruction of the laminate is done by crushing the modules into grains of ≤20mm. The particles must be small enough for the attrition to be affective. To achieve small uniform pieces the CIS must be put through a shredder, rotating shear and impact pin mill.[26]
Separation of Semiconductor layer
The separation of the semiconductor layer is done be two different processes depending on in the module has been broken or not. For a module with intact carrier glass the process calls for vacuum blasting. This is a special blasting technique as it uses a vacuum instead of air pressure. This minimizes dust emissions and enables a closed circuit of the blasting medium. For the broken modules Atrittion will be used. The crushed material is put into containers where it is stirred and shearing forces are applied. The shearing forces can remove the modules layers without the addition of any chemicals.[26]
Flotation
Enrichment of the semiconductor material is done by flotation. This separates the various materials from one another. This step uses a series of different flotates and centrifugal forces to filter out the impurities[26]The advantages with this procedure include a safer process and the use of very few chemicals. This process uses frictional forces to separate the different materials which means no chemicals are used in the separation process. Without the use of hazardous chemicals one can expect the safety related cost to be decreased. Depending on the final use of the materials there might be less need for further treatment using this process.The percent valuables yield for this process were just 35.26%.[26]
Chemical Separation Process[edit | edit source]
For the process of separating the layers of the PV modules chemically, a module pre-treatment must be done first. This pretreatment is simply crushing up the material to a small size, similiar to that of the wet process discussed above. This will speed up the reaction process and increase efficiencies on account of increased exposed surface area.
First the cells are treated with a nitric acid based lixivant. The lixivant selectively oxidizes and solubilizes the copper, indium, selenium, and zinc. The Sn02 conducting layer remains intact on the glass substrate. The EVA plastic from the laminate will be hydrolyzed and float to the top of the lixivating solution where it can be retrieved for disposal. EVA requires no further treatment and can be disposed.
A full scale process would be conducted in a trough with several electrodes to remove the Cu, Se, and Cd. In this trough the Cu and Se will be attracted to the electrodes nearest the solution inlet and the Cd will accumulate on the electrodes closest to the solution outlet. Decomposition of the lixivant will yield Indium, Zinc, and residual metal oxides.[27]They can then be sold to a refiner for further solvent extraction.

Safety[edit | edit source]
When starting any industrial process environmental, health and safety issues must be addressed. The safety and end of life analysis will be addressed in this section of the project. Federal and California State environmental were taken into consideration for the report used in this project.
For the mechanical recycling process we have looked into, the separation of the PV module is done primarily by crushing and shearing forces. This process seemed to be the best from an environmental standpoint. The only additional safety concerns due to this process are concerns that must be dealt with whenever heavy machinery is present so it will not be outlined in this section. For a chemical separation process crushing is still done to pre-treat the modules so any concerns with heavy machinery must still be addressed. In addition to the machinery for the chemical process nitric acid is used in the chemical separation process. Safety plans must be put in place for this chemical and any other byproducts produced through this process. Safety pals will vary for each process and will be required for any plant developed.
CIS PV material going through certain reclamation processes will likely be considered non-hazardous under Federal and California State regulations. End of life CIS PV material will in most cases be unregulated non-hazardous trash. Defective CIS plates will likely be exempt from federal regulation and can probably undergo in-house separation and pre-treatment for reclamation.[28]
With most CIS modules not being classified as hazardous at the end of their life it becomes easier to transport and process these materials. The only problem with that is because the concentration of the potentially harmful materials are so low there won't likely be any reason to recycle to avoid costly or cumbersome disposal. In the case of a CIS PV module recycling plant the modules taken in by the plant would be exempt from being considered waste.[28] Due to the information listed above the CIS modules that will be dealt with by an outside recycling plant will likely be exempt from hazardous waste regulations. This will likely be true for both defective and end of life modules. This can greatly reduce the cost when planning a CIS photovoltaic recycling plant but one must still take into account the toxic or possibly harmful chemicals that are contained in CIS modules.[28]CIS modules contain an array of potentially harmful materials; however these chemicals are in small amounts. Cadmium is the most harmful of these materials;[29] with the use of cadmium becoming more restricted we have decided to forgo the explanation and problems with this element. Other possible harmful materials associated with CIS modules include selenium, molybdenum, and indium. These are some of the materials that will have to be planned for when starting a recycling plant. The concentration of these materials is such that in most cases there will be minor potential for safety or heath related problems. Reverse logistics companies are already in place to collect, consolidate and transport to manufacturers and recyclers.[28]Safety concerns in the transportation of these modules can be viewed as small due to the facts that there is already an infrastructure in place and the material will likely be considered non-hazardous.
MSDS[edit | edit source]
Nitric acid
Copper (II) Chloride Dihydrate
Indium Trichloride
Selenious acid
Hydrochloric acid
Copper
Indium
Selenium
Cadmium Sulfide
Zinc Oxide
Molybdenum
Thiourea
Capital Equipment[edit | edit source]
Assuming that a photovoltaic manufacturing plant capable of producing enough solar modules to produce 1GW of power will produce 200000 tons of solar modules along with 10000 tons of waste material annually we can find equipment needs. From past reports and experiments on the subject we have found that most of the waste produced in this process can be recycled in house. So if we assume that all modules from this plant will be recycled at the end of life we can expect roughly 200000 tons of waste yearly, keeping in mind that no plant of this size has been built and it doesn't seem likely that one will be built relatively soon. From this we could expect raw materials entering the plant daily to be around 550 tons. This is assuming that the plant would run 365 days a year.
Capital equipment needed for wet-mechanical process, capable of treating 600 tons of PV material daily
Crushing Mill – capable of crushing glass laminate
Industrial furnaces - the actual size of the furnaces will change depending on hours of on time, time to treat PV material which is unknown (only experiments were done on extremely small material volumes so it would be unrealistic to base numbers off values in this experiment), and material density which is roughly 2650 kg/m3.
Shredder, Rotating Shear, Impact Pin Mill – capable of producing uniform glass grains
Vacuum blaster – very little is known on the specifications needed for the vacuum blaster.
Flotation system – multistep flotation system with large rotating drums and varying filters for different materials
Capital equipment for Chemical separation process, capable of treating 600 tons of PV material daily
Crushing Mill – capable of crushing glass laminate
Mixing tanks - capable of holding and mixing PV materials with nitric acid
Electrolysis System – Trough like configurations with several electrodes capable of removing metals
Vacuum hood – capable of removing any harmful gases from chemical separation process
Other than the equipment listed all health and safety equipment will rely on OSHA standards
References[edit | edit source]
- ↑ A. Rockett, R.N. Bhattacharya, V. Kapur, S.H. Wei, Basic Research Opportunities in CU-Chalcopyrite Photovoltaics, April 1999, NREL/CP-520-29587
- ↑ Kemell, M., Ritala, M., & Leskelä, M. (2005). "Thin film deposition methods for CuInSe2 solar cells". Critical Reviews in Solid State and Materials Sciences, 30(1), 1-1-31. Retrieved from Proquest.
- ↑ 3.0 3.1 U.S. Department of Energy, Copper Indium Diselenide - as a Photovoltaic Material, January 2002.
- ↑ Solar Facts & Advice, Alchemie Limited Inc. (http://www.solar-facts-and-advice.com/CIGS-solar-cell.html)
- ↑ 5.0 5.1 5.2 Bernhard Dimmler, Rolf Wächter, Manufacturing and application of CIS solar modules, Thin Solid Films, Volume 515, Issue 15, 31 May 2007, Pages 5973-5978, ISSN 0040-6090, 10.1016/j.tsf.2006.12.150.
- ↑ Zhang Xuan, Rajendiran Aravind Raj, Wu Yiming., CIGS Solar Cells: How and Why is their Cost Falling?
- ↑ Green, M. A. (2006), Consolidation of thin-film photovoltaic technology: the coming decade of opportunity., Progress in Photovoltaics: Research and Applications, 14: 383–392. doi: 10.1002/pip.702
- ↑ Udai P. Singh and Surya P. Patra, Progress in Polycrystalline Thin-Film Cu(In,Ga)Se2 Solar Cells, International Journal of Photoenergy, Volume 2010, Article ID 468147, 19 pages doi:10.1155/2010/468147
- ↑ A.E. Delahoy, J.S. Britt, and Z.J. Kiss;, CIS Photovoltaic Technology, October 1998, NREL/SR-520-25713
- ↑ 10.0 10.1 10.2 10.3 10.4 K. L. Chopra, P. D. Paulson, and V. Dutta, Thin-Film Solar Cells: An Overview, Prog. Photovolt: Res. Appl. 2004; 12:69–92 doi: 10.1002/pip.541
- ↑ 11.0 11.1 T.J Gillespie, C.H Marshall, M Contreras, J Keane, Copper indium diselenide (CIS) process, control and manufacturing, Solar Energy Materials and Solar Cells, Volume 59, Issues 1-2, September 1999, Pages 27-34, ISSN 0927-0248, 10.1016/S0927-0248(99)00028-8.
- ↑ 12.0 12.1 12.2 M.E Calixto, P.J Sebastian, R.N Bhattacharya, Rommel Noufi, Compositional and optoelectronic properties of CIS and CIGS thin films formed by electrodeposition, Solar Energy Materials and Solar Cells, Volume 59, Issues 1-2, September 1999, Pages 75-84, ISSN 0927-0248, 10.1016/S0927-0248(99)00033-1.
- ↑ 13.0 13.1 Franz H Karg, Development and manufacturing of CIS thin film solar modules, Solar Energy Materials and Solar Cells, Volume 66, Issues 1-4, February 2001, Pages 645-653, ISSN 0927-0248, 10.1016/S0927-0248(00)00256-7.
- ↑ P.J Sebastian, M.E Calixto, R.N Bhattacharya, Rommel Noufi, CIS and CIGS based photovoltaic structures developed from electrodeposited precursors, Solar Energy Materials and Solar Cells, Volume 59, Issues 1-2, September 1999, Pages 125-135, ISSN 0927-0248, 10.1016/S0927-0248(99)00037-9.
- ↑ 15.0 15.1 15.2 Green MA, Emery K, King DL, Igari S, Warta W. Solar cell efficiency tables (version 21). Progress in Photovoltaics: Research and Applications 2003; 11: 39–45
- ↑ 16.0 16.1 Chris Eberspacher, Chris Fredric, Karen Pauls and Jack Serra; Thin-film CIS alloy PV materials fabricated using non-vacuum, particles-based techniques, Thin Solid Films, Volume 387, Issues 1-2, 29 May 2001, Pages 18-22, ISSN 0040-6090, 0.1016/S0040-6090(00)01729-6.
- ↑ Jörg Palm, Volker Probst, Franz H. Karg, Second generation CIS solar modules, Solar Energy, Volume 77, Issue 6, December 2004, Pages 757-765, ISSN 0038-092X, 10.1016/j.solener.2004.05.011.
- ↑ Strand, T.; Kroposki, B.; Hansen, R.; Willett, D.;, Siemens solar CIS photovoltaic module and system performance at the National Renewable Energy Laboratory, Photovoltaic Specialists Conference, 1996., Conference Record of the Twenty Fifth IEEE, vol., no., pp.965-968, 13-17 May 1996 doi: 10.1109/PVSC.1996.564290
- ↑ M. Powalla, G. Voorwinden, D. Hariskos, P. Jackson, R. Kniese,Highly efficient CIS solar cells and modules made by the co-evaporation process, Thin Solid Films, Volume 517, Issue 7, 2 February 2009, Pages 2111-2114, ISSN 0040-6090, 10.1016/j.tsf.2008.10.126.
- ↑ Green MA, Emery K, King DL, Igari S, Warta W. Solar cell efficiency tables (version 36). Progress in Photovoltaics:Research and Applications 2010,18:346–352
- ↑ 21.0 21.1 Paifeng Luo, Ruzhong Zuo, Litao Chen, The preparation of CuInSe2 films by combustion method and non-vacuum spin-coating process, Solar Energy Materials & Solar Cells, 94(2010) Pages 1146–1151
- ↑ M. Kaelin, D. Rudmann, F. Kurdesau, T. Meyer, H. Zogg, A.N. Tiwari, CIS and CIGS layers from selenized nanoparticle precursors, Thin Solid Films, Volumes 431-432, 1 May 2003, Pages 58-62, ISSN 0040-6090, 10.1016/S0040-6090(03)00194-9
- ↑ 23.0 23.1 23.2 23.3 23.4 Marco Raugei, Silvia Bargigli, Sergio Ulgiati, Life cycle assessment and energy pay-back time of advanced photovoltaic modules: CdTe and CIS compared to poly-Si, Energy, Volume 32, Issue 8, August 2007, Pages 1310-1318, ISSN 0360-5442, 10.1016/j.energy.2006.10.003.
- ↑ Thumm, W.; Finke, A.; Neumeier, B.; Beck, B.; Kettrup, A.; Steinberger, H.; Moskowitz, P.D.;,Environmental and health aspects of CIS-module production, use and disposal,Photovoltaic Energy Conversion, 1994., 1994 IEEE First World Conference on, vol.1, no., pp.262-265 vol.1, 5-9 Dec 1994, doi: 10.1109/WCPEC.1994.519858
- ↑ 25.0 25.1 25.2 25.3 25.4 Vasilis M. Fthenakis, End-of-life management and recycling of PV modules, Energy Policy, Volume 28, Issue 14, November 2000, Pages 1051-1058, ISSN 0301-4215, 10.1016/S0301-4215(00)00091-4.
- ↑ 26.0 26.1 26.2 26.3 26.4 Wolfgang Berger, Franz-Georg Simon, Karin Weimann, Erik A. Alsema, A novel approach for the recycling of thin film photovoltaic modules, Resources, Conservation and Recycling, Volume 54, Issue 10, August 2010, Pages 711-718, ISSN 0921-3449, 10.1016/j.resconrec.2009.12.001.
- ↑ Goozner, R.E.; Drinkard, W.F.; Long, M.O.; Byrd, C.M.;, A process to recycle thin film PV materials, Photovoltaic Specialists Conference, 1997., Conference Record of the Twenty-Sixth IEEE, vol., no., pp.1161-1163, 29 Sep-3 Oct 1997 doi: 10.1109/PVSC.1997.654295
- ↑ 28.0 28.1 28.2 28.3 C. Eberspacher, V. M. Fthenakis* and P. D. Moskowitz; Environmental, Health and Safety Issues related to commercializing CuInSe2 Photovoltaics, July 1996, Brookhaven National Laboratory, BNL-63334.
- ↑ P.D Fthenakis, V. M. Moskowitz,Photovoltaics: Environmental, Health and Safety Issues and Perspectives, Progress in Photovoltaics (2000), Vol 8; Part 1, pages 27-38
- ↑ Ermer, J.; Gay, R.; Pier, D.; Tarrant, D.;, Challenges and progress in the scale up of CuInSe2 thin film photovoltaic technology, Journal of Vacuum Science & Technology A: Vacuum, Surfaces, and Films, vol.11, no.4, pp.1888-1895, Jul 1993 doi: 10.1116/1.578518
- ↑ T. Todorov,E. Cordoncillo,J. F. Sánchez-Royo,J. Carda, and,P. Escribano,CuInS2 Films for Photovoltaic Applications Deposited by a Low-Cost Method, Chemistry of Materials 2006 18 (13), 3145-3150