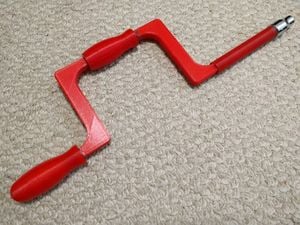
This project stems from the OXFAM equipment catalog and attempts to make a 3D printed version of a speed brace. The purpose of this tool is to quickly remove fasteners after they have been broken loose using a breaker bar or ratchet. This tool is meant to be used with 1/2" drive sockets.
Bill of Materials[edit | edit source]
Here is a bill of materials. Costs are based on a $20.00 / Kg of PLA filament price:
Quantity | Part Name | Material (grams) | Cost ($) | Total ($) |
---|---|---|---|---|
2 | Corner Joined | 57.00 | 1.14 | 2.28 |
1 | Coupling | 21.00 | 0.42 | 0.42 |
1 | Coupling Handle | 14.00 | 0.28 | 0.28 |
1 | Drive | 11.00 | 0.22 | 0.22 |
1 | Handle | 31.00 | 0.62 | 0.62 |
1 | Handle End | 59.00 | 1.18 | 1.18 |
1 | Key Long | 4.00 | 0.08 | 0.08 |
1 | Key Short | 2.00 | 0.04 | 0.04 |
Total Cost | $5.12 |
All STL files as well as source files can be found at youmagine.com [1]
Tools needed[edit | edit source]
- MOST Delta RepRap or similar RepRap 3-D printer
- Hobby knife for print cleanup
- Hammer
Skills and knowledge needed[edit | edit source]
Technical Specifications and Assembly Instructions[edit | edit source]
Recommended Print Settings[edit | edit source]
All STL files are orientated for printing. Print all objects according to the quantities listed in the BOM (Two "Joined_Corner" pieces are required).
- Layer Height: 0.25 mm
- Infill: 100%
- Support Material: None
- Shell Thickness: 2 lines
- Print Temp: 210 Degrees Celcius
- Print Time: Approx. 10 Hours
Part Preparation[edit | edit source]
- Clean all mating edges with a hobby knife. Be careful not to take too much off.
- Test fit parts while prepping the matting edges.
- If parts get stuck together use a 1/2" wrench and hammer to separate them.
- Parts should fit snugly together so that small taps with a hammer will seat the parts together.
Assembly[edit | edit source]
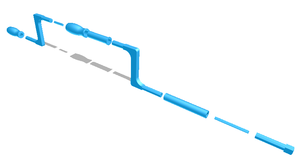
- Approximate Assembly Time: 30 Minutes
- After all parts are prepped lay them out as in the figure to the right.
- (Optional) Apply JB Weld or similar two part epoxy to all joints.
- Make sure the fat end of the handle is away from the drive end.
- Seat all parts with a hammer.
Common Problems and Solutions[edit | edit source]
- If 100% Infill does not provide enough strength there are a few options.
- Epoxy all joints
- Try an alternate print material
- Future consideration: may redesign with an overall larger cross section area.
Cost savings[edit | edit source]
Commercial Equivalent[edit | edit source]
A 1/2" drive speed brace can be purchased for $41.08 from [2]
Savings in Dollars[edit | edit source]
Given the print cost of $5.12 shown in the BOM and the cost of the commercial equivalent being $41.08, the savings are $41.08 - $5.12 = $35.96 Savings
Savings in Percent[edit | edit source]
Given the dollar savings of $35.96 calculated above and the cost of the commercial equivalent being $41.08, the percentage savings are ($35.96 / $41.08) *100 = 87.54 % Savings
References[edit | edit source]
The following website was used to obtain dimensions for the 1/2" socket drive: Engineers Edge - Standard Square Drives for Socket Tools, ASA B5.38 (1958) Available: http://www.engineersedge.com/hardware/square-drive-tools.htm