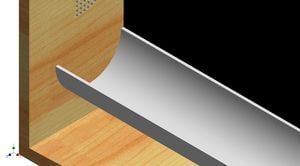
An abundance of clean, locally-produced, combustible fuel could dramatically improve the standard of living in parts of the developing world. This fuel could transport goods to markets, produce steam and electricity, heat homes, boil water and cook food, provide power for communication equipment and provide for better standards of education and health. With less reliance on dirtier fuels, there would be less air pollution indoors and out, less deforestation and erosion of soils. This report describes the simple engineering required to increase the efficiency of a solar still to produce low-cost, concentrated ethanol for fuel at the local, "micro" level, reliably and safely.
It should be noted that this project is for fuel-alcohol only, and not for human consumption, though the basic design principles could be applied to distillation of water or other liquids. It should also be noted that this is a theoretical design at this point and as such no prototyping or testing has been done, but the results of said testing will be posted when they are available.
History[edit | edit source]
Over the last two centuries, many systems for generating alcohol fuel (ethanol) from sugars and starches have been developed and inventors have demonstrated the utility of this fuel. The first alcohol-fuelled engine was an internal combustion engine, built in 1826 by Samuel Morey.[1] Fifty years later, German engineer Nicholas Otto invented the four-stroke (Otto Cycle) internal combustion engine, using ethanol as its primary fuel. In the late 1800's, Henry Ford's Quadricycle ran on ethanol. He believed that alcohol was "the fuel of the future" and, in 1912, made his Model-T available with an ethanol engine. Farm equipment in Europe was developed using ethanol for fuel throughout the 20th century, increasing these countries' self-reliance. Disruptions to North American petroleum supplies from the Middle East began in the early 1970's and, in response to these supply problems, public policy has encouraged research and development into alternative fuels as a way to escape dependence on hostile suppliers.
In a report published by the National Center for Appropriate Technology in 1981, Bradley, Moody, Portch and Runnion created a summary of the common available technologies for producing alcohol fuels from sugars and starches.[2] Since this time, technologies for alcohol fuel production have become increasingly complex, making them less available where cost and simplicity of design are important.
Fuel vs. Food Controversy[edit | edit source]
The desirability and ethics of ethanol production from materials which could serve as food is the subject of increasing controversy and debate. What is not debated, however, is the profound, positive effect on local economies, manufacturing, environments and standard of living the expanded use of these clean fuels could have in developing communities and nations. The ultimate answer to this debate may lie in the development of low-cost production of fuel-alcohol from cellulose and hemi-cellulose but, until this technology becomes more readily available and affordable, engineering may be able to bridge the gap between potential and real benefits using current knowledge.
Background[edit | edit source]
Available sources of fuel substrates[edit | edit source]
The conversion of sugars and grains and non-edible plant material (cellulose and hemi-cellulose) to ethanol is accomplished through the three-steps of hydrolysis, fermentation and distillation. A short description of these processes are offered here but a more detailed description of hydrolysis entitled "Starch hydrolysis for ethanol production." by G.B. Borglum of Myles Laboratories is available here, while a good review of fermentation is found here. A particularly good article describing solar distillation can be found here.
Hydrolysis[edit | edit source]
Fruits, vegetables and grains, all sources of sugars and starches, are boiled and agitated for 30 minutes to break down cell walls, releasing long-chain sugars. Inexpensive and commercially available alpha-amylase is added to the solution, as it cools, to hydrolyse these long-chain sugars to short-chain polysaccharides. Next, beta-amylase is added to this solution to reduce short-chain sugars to individual glucose molecules. This process is reasonable for remote and developing communities because the costs and requirements for this technology are small.
If non-edible plant cellulose and hemi-cellulose such as cane or corn stalks or wood fibre, amongst many others, are to be used, they are also boiled to release a variety of polysaccharides. At that point, more sophisticated chemicals in the form of cellulases, derived from various organisms, are used to convert these long-chained sugars to simple monosaccharides.[3] These simple sugars include xylose, manose, galactose and pentose sugars, amongst others. Chemical hydrolysis of cellulose and hemi-cellulose by strong acids (H2SO4, HCl) can also be used to expose sugars.[4]
Fermentation[edit | edit source]
If the solution contains simple glucose, brewer's yeast (Saccharomyces cerevisiae) is added and the solution is agitated to oxygenate it for ten to twenty minutes, initiating the budding of the yeast. Saccharomyces will ferment glucose in oxygen but will do this more completely in anaerobic conditions. The solution is isolated from the air, and CO2 and ethanol are produced. As was discussed under hydrolysis, if sugars other than glucose (those derived from cellulose and hemi-cellulose) are present, other enzymes are required. Xylose is the predominant monosaccharide from cellulitic hydrolysis, therefore, beta-D-xylosidases are commonly used.[5] The introduction of organisms that produce these enzymes in anaerobic conditions, results in the production of a variety of by-products, primarily, but not exclusively, CO2 and ethanol.
The ethanol in the "beer" produced in either process will increase in concentration until the sugars in the solution are exhausted or the ethanol concentration exceeds the tolerances of the organisms being used for fermentation and they are killed. This usually occurs above 14%. Most fermentation processes will use a hydrometer to guide the decision as to when to extract the fermented product, usually at concentrations of 10 to 12% so that new substrate can be added, diluting the concentration and allowing the process to continue without killing the essential organisms.
Distillation[edit | edit source]
Ethanol is miscible in water and the solution can be concentrated by distillation to levels where it can function as a fuel, a mixture of 50% or greater. The potential of the solution to be used as fuel increases as the concentration increases. Because alcohol and water become an azeotrope at an ethanol concentration of about 95%, distillation to this concentration is the ideal, as controlling the pressure inside the still is beyond the scope of this design.
Ethanol will separate from the mixture when the temperature of the vaporizing chamber reaches the boiling point of the ethanol, (a table of evaporation temperatures can be found in Table 1). The temperature of evaporation for the ethanol-water solution will be between the boiling point of ethanol and that of water, dependent on the concentration of the solution.
Stills that are capable of producing highly concentrated ethanol do so by remaining at the boiling temperature of pure ethanol.
Table 1 - Boiling point of 95% ethanol vs. altitude
Altitude (ft) | Boiling point of 95% ethanol (°C) |
0 | 78.1 |
500 | 77.3 |
1000 | 77.1 |
1500 | 76.7 |
2000 | 76.2 |
2500 | 75.7 |
3000 | 75.2 |
3500 | 74.7 |
4000 | 74.2 |
4500 | 73.8 |
5000 | 73.3 |
6000 | 72.4 |
7000 | 71.4 |
8000 | 70.4 |
9000 | 69.4 |
10 000 | 68.4 |
15 000 | 63.5 |
High Grade Fuel from Low Technology[edit | edit source]
Solar stills are minimally sophisticated devices that employ solar energy to separate ethanol from the water in the solution. Short-wave, UV radiation penetrates the glass on the face of the still, hits the dark surface of the evaporation wick and is converted to longer-wave radiation, becoming trapped in the still and heating it (green-house effect). The ethanol vapor rises from the evaporation pad, contacts the glass on the front of the still, condenses and collects in a concentration exceeding that of the original solution. Initially, the still will warm to the boiling point of the ethanol and the majority of the distillation will take place relatively quickly, but as the ethanol is extracted and the composition of the water mixture changes, the temperature inside the still will increase, eventually reaching a point where some of the mixture will begin to boil. In practice, this results in a concentration of close to 60% from an initial batch of 10% ethanol solution. Further distillation runs will eventually yield a 95% solution.
Build[edit | edit source]
While the design has not been tested as of yet, the still in this project should, in theory, work as both a batch and continuous still. It also provides the option for an actively controlled air vent to be added to help control the internal temperature. Figure 1 below shows the still's basic design and proposed dimensions. The internal dimensions were chosen based on the requirement of the still to be able to process a batch size of 1 Litre. Based on standard diameter plastic pipes and what were deemed reasonable dimensions for construction, an optimal pipe diameter and length were chosen to be 3 inches and 20 inches respectively, and as such internal dimensions measure 20" x 20" x 4.5".
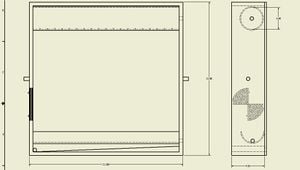
Materials[edit | edit source]
- Materials for sides (suggested: 4.5" x 3/4" wood or otherwise)
- Material to make angled base piece (use end cut of side material)
- Material to make vent cover (use end cut of side material)
- Material to cover the back-plate of the still (1/4" plywood or equivalent)
- Burlap or other dark wicking material
- Two 3" inner diameter, 20" long pieces of PVC pipe
- Two screws
- Two bolts and corresponding drill bit for mounting the still to a stand
- One piece of Plexiglass large enough to cover the box's front face
- 1/16" Drill bit or equivalent for making holes in the PVC pipe
- 1/4" Drill bit for making vent holes.
- Black paint (optional)
- Stand material (not covered in this project).
Assembly
[edit | edit source]
Operation[edit | edit source]
If the still is being operated using a batch of fluid, fill either the top pipe or the collection trough with 10% ethanol/water solution. Depending on where the fluid is input, it will soak down or wick up the material on the back-plate, which gives it a much greater area to evaporate from. The ethanol will begin to evaporate as the still heats up and it will condense on the Plexiglas. Once condensed, the ethanol will run down to the slanted base-piece where it can be collected via the hole in the back of the still and either used directly if the concentration is correct, or reprocessed if not. If the top pipe was filled with the batch, or if the still is being used in a continuous distillation process, the fluid in the collection trough can be collected for reprocessing, cascaded into a second still, or discarded.
Future Work[edit | edit source]
Future work for this project includes prototyping and field testing the unit starting with a 10% ethanol-water mixture. Once a baseline of the unit's distillation efficiency is obtained, the active temperature-control system should tested. Once the ability of the still to be temperature is demonstrated, a true passive temperature-control system should be designed, built and field-tested. Another addition to the project should be to create picture instructions for non-english speaking users.
References[edit | edit source]
- ↑ Hardnburg, H. O. Samuel Morey and His Atmospheric Engine. Warrendale, PA: Soc. Automot. Engineers, 1992, p. 6-7.
- ↑ Bradley, C., R. Moody, R. Portch and K. Runnion. Fuel alcohol production: a selective survey of operating systems. National Center for Appropriate Technology, 1981. p.48.
- ↑ Binder, J.B. and R.T. Raines. Fermentable sugars by chemical hydrolysis of biomass. Proceedings of the National Academy of Sciences of the United States of America, January, 2010.
- ↑ Rumbolt, K., van Buijsen, H.J.,Overkamp, K.M., van Groenestijn, J.W., Punt, P.J., and van der Werf, M.J. Microbial production host selection for converting second-generation feedstocks into bioproducts. Microb Cell Fact., 2009. Dec 4; 8:64.
- ↑ Selig, M.J. et al. Heterologous expression of Aspergillus niger B-D-xylosidase: Characterization on lignocellulosic substrates. J. Appl. Biochem. Biotech. Vol 146, #1-3/March, 2008.