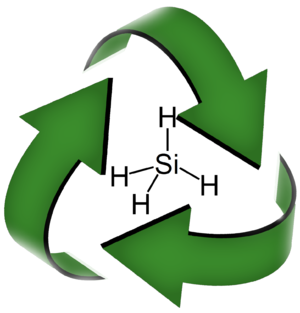
Amorphous silicon (a-Si:H)-based solar cells have the lowest ecological impact of photovoltaic (PV) materials. In order to continue to improve the environmental performance of PV manufacturing using proposed industrial symbiosis techniques, this paper performs a life cycle analysis (LCA) on both conventional 1-GW scaled a-Si:H-based single junction and a-Si:H/microcrystalline-Si:H tandem cell solar PV manufacturing plants and such plants coupled to silane recycling plants. Both the energy consumed and greenhouse gas emissions are tracked in the LCA, then silane gas is reused in the manufacturing process rather than standard waste combustion. Using a recycling process that results in a silane loss of only 17% instead of conventional processing that loses 85% silane, results in an energy savings of 81,700 GJ and prevents 4400 tons of CO2 from being released into the atmosphere per year for the single junction plant. Due to the increased use of silane for the relatively thick microcrystalline-Si:H layers in the tandem junction plants, the savings are even more substantial – 290,000 GJ of energy savings and 15.6 million kg of CO2 eq. emission reductions per year. This recycling process reduces the cost of raw silane by 68%, or approximately $22.6 million per year for a 1-GW a-Si:H-based PV production facility and over $79 million per year for tandem manufacturing. The results are discussed and conclusions are drawn about the technical feasibility and environmental benefits of silane recycling in an eco-industrial park centered around a-Si:H-based PV manufacturing plants.
See also[edit | edit source]
- Life cycle analysis of semiconductor recycling in thin film photovoltaic manufacturing methods
- Life cycle analysis of semiconductor recycling in thin film photovoltaic manufacturing literature review
- Is small or big solar better for the environment? Comparative life cycle assessment of solar photovoltaic rooftop vs. ground‑mounted systems
- Environmental Life Cycle Analysis of Manufacturing Options for Humanitarian Supplies: Drinking water containers