This is a speculative class project and needs to be refined before being deployed at any scale.
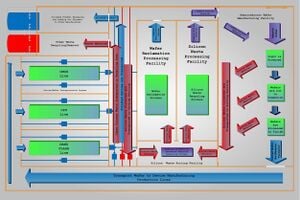
One of the hottest products on the market is currently the Apple iPhone. Media hype is generated on a daily basis concerning the iPhone, its features, and the company that makes it. The iPhone is a "smartphone" with capabilities beyond that of a simple cell phone. In addition to making simple phone calls and sending text messages, iPhone owners enjoy the convenience of being able to send and receive email, surf the internet, video call other iPhone owners, and a plethora of other functions. Unfortunately, like with most electronics, with the release of the new iPhones previous generations are quickly discarded. The (Apple iPhone 4S) is no exception. With the release of the Apple iPhone 5, iPhone enthusiast will undoubtedly move on to the new generation, leaving the iPhone 4S behind.
The question then becomes, what will happen to the outdated iPhone 4S? The answer is, hopefully, that it will be recycled. This where this project comes into play. While recycling is not a new concept to many, the means by which different material is recycled may be a little less familiar. In order to shine some light on this matter, this project gives a brief overview of what could be considered when the attempt of recycling the iPhone 4S is pursued.
In order conduct a more in depth analysis, the scope of this this project has been limited to the recycling of the components consisting of semiconductorW material. In the case of the iPhone 4S, the semiconductor material of interest is silicon.
The reason for this is that silicon is the base material used in nearly all electronic devices. Initially processed from sand (SiO2), the silicon is placed into a crucible where it is heated up to just above its melting temperature, approximately 1600 degrees Celsius. When completely melted, a rod containing a "seed" of single crystalline silicon (Si)W is then placed into the is immersed into the crucible of molten silicon. As the rod is slowly spun and removed from the crucible, a nearly perfect silicon crystal is formed. This process is refered to as the Czochralski processW. This large crystal is then checked for impurities and sliced into the wafers. These wafers are then processed to make silicon chips; a processes outlined in a clip from the Science Channel show How Do They Do It?, shown below.
With this in mind, the following semiconductor containing components were chosen for this project:
- Apple 5 (S5L8940) Dual-core processorW – PoPW featuring: Elpida B4064B2PF-8D-F –Elpida 512 MB of Low-power DDR2 DRAM
- Toshiba THGVX1G7D2GLA08 16GB 24nm MLCW NAND Flash Memory W
- iSight camera
Because the group was not willing to tear apart their phones in the pursuit of discovering what components are used in the iPhone 4S, they utilized ifixit.com's iPhone 4S Teardown[1] in the exploration of the Apple iPhone 4s hardware.
At this point it should be noted that a more in depth exploration into the production of the silicon wafer is outlined below under the Manufacturing Process section 2.7.1.
Current and Future Market Scope[edit | edit source]
To determine the current number of Iphone 4 & 4S model in the market official Apple press releases were used along with other financial articles when needed.
iPhone 4 introduction date: June 24th, 2010. Which falls under Apple's fiscal 3rd quarter for 2010.
iPhone 4S introduction date: October 11th, 2011. Which falls under Apple's fiscal 4th quarter for 2011.
Total Volume of Iphone 4/4S Models Sold to Date | Fiscal Year | Quarter | iPhone 4/4S Volume (units) | ||
---|---|---|---|---|---|
2010 | Q3 | 1,700,000[2][3] | |||
2010 | Q4 | 14,100,000[4] | |||
2011 | Q1 | 16,240,000[5] | |||
2011 | Q2 | 18,650,000[6] | |||
2011 | Q3 | 20,340,000[7] | |||
2011 | Q4 | 13,070,000 (iPhone 4)[8][9] | 2012 | Q1 | 37,040,000[10] |
2012 | Q2 | 35,100,000[11] | |||
2012 | Q3 | 26,000,000[12] | |||
2012 | Q4 | 18,000,000 - 22,000,000(estimate)[13]
16,000,000 - 18,000,000(estimate)[14] | |||
Iphone 4/4S Totals: | 84,100,000 (iPhone 4 Only)
102,140,000 (iPhone 4S Only - excluding Q4 2012 Est.) 186,240,000 (Combined - excluding Q4 2012 Est.) 202,240,000 - 208,240,000 (Combined - including Q4 2012 Est.) |
The table above represents sales for Apple, Inc's fiscal calendar year (i.e. Apple's Q4 ends on October 18th).
With the release of the iPhone 5, the sales expectation of the iPhone 4S is expected to be 15-20% of total iPhone sales thru Q3 2013. This expectation is due to the decrease in the cost of the iPhone 4S by carriers along with the fact that the iPhone 4S supports iOS 6 which is the current generation operating system running on the iPhone 5.
Current Recycling Practices[edit | edit source]
Apple currently runs a recycling program for all iPods, iPads, iPhones, and Macs (Desktop or Laptop) .[15] Products are sent to PowerOn, where they undergo testing to determine if the product have any monetary value. Those deemed with monetary value are refurbished and sold on secondary electronic product markets.[16] Products found to have no monetary value are sent to WeRecycle! for recycling.[17] Products received by WeRecycle undergo disassembly, then shredding. Once shredded, the products will then go through an automated sorting. The shredded parts are sorted based on what material they are made of or what type of component they are. (i.e., dark plastic, light plastic, aluminum, steel, circuit boards, "electronics", etc). For example, pieces of ferrous metals are sorted through the use of magnets. After sorting, the shredded materials are sent to their respective commodities market. The entire process is outlined in the flowchart found below. The flowchart was found on the WeRecycle webpage after scrolling to the bottom of the main page and clicking the "Our Process" link.
[17]Similar to PowerOn, Sims Recycling Solutions is one of several other companies currently recovering integrated circuits (IC). The goal of these companies is to isolate potentially reusable components that still hold value. These components, once recovered, then have the potential of being used in future products. The video below gives a brief overview of this recovery process.
Potential Semiconductor Market[edit | edit source]
With the semiconductor costs consuming over 50% of the BoM (Bill of Materials) for the majority of feature filled smartphones[18] (i.e. Droid) possibilities to re-coup the semiconductor costs within the phones seem viable due to the capital cost into the components.
Estimated BoM costs by iSuppli for the iPhone 4 and iPhone 4S were $187.51[19] and $188.00[20] respectively.
With the estimated BoM for both Iphone 4 and 4S key items appear to take the majority of the component cost. These components are:
- NAND Flash
- DDR2 Ram
- CPU/Processor
- Display
- CMOS Sensor/Camera
In order to calculate the amount of semiconductor currently in products on the market, some assumptions need to be made. First, we shall assume that the thickness of semiconductor in an integrated circuit will be roughly equal to the thickness of a silicon wafer. We make this assumption with the mindset that the sequential layers added to the wafer add an insignificant volume to the microchip. Also, we make the assumption that the Toshiba THGVX1G7D2GLA08 16GB 24nm MLC NAND RAM is about equal size to the A5 processor found in the iPhone 4S. We make this assumption from looking at photos of the two chips in the phone. This assumption must be made due to a lack of sufficient information available to the public regarding the Toshiba THGVX1G7D2GLA08 16GB 24nm MLC NAND RAM.
Number of iPhone 4S on the market (estimate, using 4Q sale estimate): 205,240,000 units
Typical Thickness of Silicon Wafer: 0.004 cm-0.01 cm thick,[21] this averages to 0.007 cm thick
Silica Density: 2.65 g/cm3
Die Area: 122.20 mm2(1.2220 cm2)[22]
Multiplying the die area by the thickness, the product is the volume of semiconductor in the chip. Multiply the volume by the density yields the amount of mass in each chip. Multiply the mass by 2 (for two major chips in each phone), and then by the number of units. Upon these calculations, it is found that the amount of recyclable semiconductor in the market for the Toshiba THGVX1G7D2GLA08 16GB 24nm MLC NAND RAM and A5 Processors to be 9304801.69 grams, or 9304.8 kilograms.
Using the average silicon wafer thickness calculated and Silica density given previously, the amount of semiconductor material that could possibly be reclaimed in the iSight/OmniVision OV8830 CMOS Camera is calculated using the following.
Die Dimension(L,W): 6.410 mm, 5.940 mm[23] Die Area(LxW): 6.410 mm x 5.940 mm = 38.08 mm2
Multiplying the 38.08 mm2 die area by the average thickness for a silicon wafer of 0.07 mm, then taking the answer and converting to mass using the density of silica. For one CMOS sensor, it has a total of 0.0071 grams of semiconductor in it. For the total market of 205,240,000 iphones (1 per iphone) the total would be 1449.78 kg of semiconductor material.
Combined the NAND, CPU, and CMOS sensor would equal a total of 10754.58 kg for the total iPhone 4/4S market.
Post Consumer Recycling Viability?[edit | edit source]
As processing/production of semiconductors have increased efficiency through new methods, better process controlling, semiconductor design; the manufacturing of these components still eat up the majority of the Bill of Materials (BoM). Being able to reuse or recycle current components with existing models could dramatically reduce costs including repair/refurbishment of the existing model. Re-purposing the cpu, nand and ram memory of the units for other devices is possible as well.
The group thinks that the recycling of the semiconductor material during and post life of the iPhone 4/4S is not viable. This is due to in the previous sections, calculations used apple press releases for unit volume of the iPhone 4. Of that roughly 85,000,000 (iPhone4) units it is estimated that only 10-25% of the total number of devices would actually be recycled, meaning that 63-77 million will end up in landfills. Recycling these devices in greater quantities could help make the recycling of them viable. As it stands due to the amount of waste or semiconductor material in cell phones they are considered a small contributor to the total amount of semiconductor waste as majority of the larger devices end up utilizing more resources so focusing on them would be the most economical/monetary solution. [verification needed]
Manufacturing Process[edit | edit source]
Components that comprise the majority of the semiconductor in the iPhone are the CPU, DDR2 Ram Memory, NAND Flash memory and CMOS Sensor(Camera) and share some similarity in the manufacturing process for each component. Worthwhile note, the BOM for the iPhone lists these as the primary expense in manufacturing of the phones.
The manufacturing of the iPhone components all start fundamentally at the same point. Which is that all of these components use electronics grade silicon(EGS) wafers as the basis prior to the actual manufacturing of each individual component.
Electronics Grade Silicon Wafer[edit | edit source]
Raw silicon, also known as metallurgical grade silicon is made through a relatively simple process. Inside a large furnace lined with carbon, Silicon dioxide (SiO2) and carbon are combined to form Silicon and Carbon monoxide, according to the chemical reaction:
SiO2 + 2C => Si + 2CO
Additional reactants are added to keep SiC from forming, which could clog the furnace. After this process, the silicon still needs to undergo several stages of purification.
The contaminated silicon is converted to Trichlorosilane in a reactor according to the following reaction:
Si + 3HCl => SiHCL3 + H2
The resulting trichlorosilne, having a boiling point of 31.8 degrees Celsius, is then distilled. Upon distillation, the trichlorosilane is converted back into high-purity silion through a Chemical Vapor Deposition (CVD) process.
During the CVD process, trichlorosilane, Cl3HSi, and doping gases like Arsine(AsH3) or Phosphine(PH3) are mixed in a reactor containing pure silicon rods, which are heated by an electric current. The following chemical reaction takes place:
SiHCl3 + H2 => Si + 3HCl
The resulting silicon will join with the silicon rods, "growing" a silicon crystal. Additionally, other reactions take place with the doping reactants causing small, precise amounts of the doping reactant to be included in the silicon crystal.[24]
Many of the gases used in or formed during the CVD process are extremely dangerous. Arsine(AsH3)and Phosphine(PH3) are both extremely poisonous. H2 and trichlorosilane are very combustible, and almost considered explosive. The resulting HCl gas formed in the reaction is very corrosive and can be more dangerous than liquid HCl.
The following image, obtained from Endress+Hauser , illustrates the process used in purifying silicon.
![]() |
"Silicon Purification" By Endress+Hauser[25] |
Once the silicon is purified, the crystall is then placed into a furnace where it is melted and processed in accordance to the process outlined in the Background section above. Further information on the purification and processing of electronic grade silicon can be found on the following company webpages:
- Green Rhino Energy, Ltd (Photovoltaic Manufacturing)
- MicroTech Systems, Inc. (Wafer Reclaiming Processing)
In-situ Recycling Potential[edit | edit source]
During the production of the Silicon wafer, precious and valuable semiconductor material is lost due to physical and chemical processes required to obtain the proper dimensions and surface finish. The group took a look at the utilization rate (the amount of semiconductor material that ends up in the final silicon wafer).
A more indepth process flow chart of the silicon wafer production process can be seen in the process flow diagram below. Observing the diagram below it can be seen, knowing that CZ-pulling referse to the Czochralski process, it can be seen that a series of material removal processing steps are required in order to make the wafer.
![]() |
"Silicon Process Flow Digram" By Dr. Helmut Föll.[26] |
Anylizing the diagram, it can be seen that the following processes are the major sources of material loss:
- Evaluation of Silicon crystal ingot; cutting off areas of poor quality or improper dimensions
- Grinding of the outer diameter to specified dimensions
- Cutting of Silicon ingot into individual wafers
- Grind of wafer edge
- Lapping or grinding of the wafer surface to flatten the surface
- Etching of the wafer
- Polishing of the wafer
As a result of these processes, 14% of the total crystal structer is lost. The additional amount of silicon that does not make it to the silicon wafer, 6% of total crystal, is left in the furnace. The locations of material loss in relation to the silicoln crystall can be seen in the figure below.
"Figure 13.3 - Graphically Representation of Silicon Waste" By Karen Reinhardt[27] |
In addition to material loss during processing, an average of 7% of the wafers break during processing. While not as significant as the material loss during processing, this scrap still has recycling potential.[28]
Taking into acount the dimentions of common silicon crystal dimentions outline in the Wikipedia page Wafer (electronics)W, the material loss is more significant than that which can be gained through post consumer recycling.
Collection Methods[edit | edit source]
Methods of collection for the waste semiconductor material, in this case Silicon is rather well defined in literature. Easiest way of collection during the manufacturing process is through the processing of the cutting/grinding/polishing lubricants found in the production process. The primary loss is through physical removal in the manufacturing of wafers. The % of the market that the collection methods are being used for are not just confined to the iPhone market but to the industry as a whole. This method of in-situ recycling appears to be much more viable.
Below is a simple flowchart that shows the processes of waste during the Silicon wafer production, emphasising the number off areas that produce waste.
The waste silicon recovery will primarilary focus on the following:
- Silicon waste water collection from material removal processes
In order to get any material out of the waste water, the water must undergo filtration. One of the handful of companies already willing to take on this task is Numero Micro Science Co., Ltd Numero has developed the "AQURUS®" which is capable of recovering over 80% of the waste water in addition to recovering over 95% lost silicon. With this machine, both the water and silicon could then potentially be purified and re-introducted back into the system on site.
- Broken wafers from device manufactures
The broken wafers collected along the production process can be collected and ground down, depending on what stage the wafer made it through before fracture. If the wafer breaks before processing, then the wafer can be ground down and placed directly back into the crucible. In the case that the wafer did undergo processing, the added layers would need to be ground off before grinding.
- Wafers from device manufactures that could be reclaimed thru polishing (non-broken)
Wafers that are found to contain defects at any given point during the chip making process are canidates for re-polishing. These, now thinner, wafers can then be used for testing instead of using a more valuable wafer.
Amount of Waste Material[edit | edit source]
Using the figure above, it is assumed that during the wafer production approximately a total 20% Silicon volume loss during ingot production occurs. Though of the 20% volume loss, the tail and shoulder accounting for 12% of the total volume of Si are able to be remelted or sold to the solar/PV industry for use in their cell as these portions generally do not meet required purity. So of the 8% total volume remains as waste in the form of pot scrap and OD grinding. The final processing of the wafer; which includes grinding and polishing from the figure above produces more volume loss. The volume loss of the ingot due to wafer process can be express through a ratio taking into account the kerf loss.
With the calculated volume percent of the ingot that becomes waste as [0.240 mm / (0.240 + 0.775 mm)] = 0.236 * 100% = 23.6% volume loss. Where the 0.240 is the kerf and the 0.775 is the thickness of the wafer So for the processing of the ingot, 23.6% of the ingot volume is produced as waste slurry.
The amount of total waste slurry will be the 8% waste in forming the ingot, with the addition of 23.6% of the ingot which represents 80% of the starting volume. So in total it is calculated as percentage; Total Slurry = 8% + 23.6%*80% = 8% + 18.8% = 26.8% total volume loss during manufacturing of wafers.
Of that total 26.8% only 90% of it will be recoverable, this is due to the silicon slurry produced during manufacturing being unable to meet the appropriate purity required for electronic grade silicon. So only 24.1% will be recoverable.
If applied to the iPhone semiconductor quantities, calculations for total energy and amount of potential reclaiming during device manufacturing assuming the 10-15% wafer breakage found in most secondary processing facilities (device manufactures).
With the calculated die sizes of 122.2 mm2, and 38.08 mm2 for the CPU/NAND and CMOS sensor, respectively. The number of 300 mm wafers needed to produce the number of devices is calculated. The group will assume a loss of 10%, since the range varies from 5-10% depending on the data source, of the total number of wafers during production due to breakage or defective processing.
The area of a 300 mm diameter wafer is calculated to be 70685 mm2. Given that approximately 15% of the wafer area is not used in device manufacturing we get an effective area of 60082 mm2.
With one(1) Cpu, NAND Flash Memory, and CMOS sensor per iPhone 4/4S; given that in prior calculations put it the production estimates put the iPhone at 205,240,000 units. So with that information the total semiconductor area is determined;
205,240,000 Iphones * [(1 CPU*122.2 mm2)+(1 NAND*122.2 mm2)+ (1 CMOS)*38.08 mm2)]
Which gives a total area of semiconductor material to be 57,976,195,200 mm2. Taking the total area and dividing by the effective wafer area, the number of wafers is determined;
57,976,195,200 mm2 / 60,082 mm2 = approx. 964,951 wafers (Assuming 300 mm Diameter wafers)
In our assumption of 10% complete wafer loss (loss due to breakage or defect during processing), total wafers required and amount completely loss is calculated;
Total Wafers = 964951 * (110%) = 1,061,446 wafers. Total Wafers 100% Lost = 964951 * (10%) = 96,495 wafers.
Determining the waste of the wafers as a function of the area. Since the total area of the wafer and the effective area is calculated, the amount of waste area per wafer is determined. Note: The 10% of processed wafers will be calculated as a 100% area loss.
Area waste per one(1)wafer = 70,685 mm2 - 60,082 mm2 = 10,603 mm2
Total area loss of wafer waste = 964,951 * 10,603 mm2 = 10,231,375,453 mm2 Total area of 100% loss processed wafers = 96,495 * 10,603 mm2 = 1,023,137,545 mm2 Combined Area Loss = 11,254,511,938 mm2
Given the density of silica at 2.65g/cm3 (0.00265g/mm3) and the previously assumed averaged thickness for a silicon layer to be 0.07 cm(0.7 mm). Volume and mass calculations are determined for the total loss. Volume is calculated as Area times the Thickness.
Volume of Lost Wafers/Waste = 11,254,511,938 mm2 * 0.07 mm = 787815835 mm3
Using the calculated volume and multiplying the value by the density for silica (0.00265g/mm3) the mass is determined;
7878158357 mm3 * 0.00265g/mm3 = 2,087,712 grams or 2,087 kg of total silicon wafer waste during processing of the wafer for devices.
Total Silicon volume need based on the volume and number of wafers and the amount of Silicon in-situ recycling.
1,061,446 300mm diameter wafers are required to produce the total number of semiconductor needed for the specified iPhone components.
The area of each wafer is 70,685 mm2, and with a thickness of 0.07 mm, the volume per wafer becomes 4948 mm3.
The combined volume of all the wafers;
4948 mm3 * 1,061,446 = 5,252,034,808 mm3
Due to the volume loss during processing the total volume required is 26.8% greater then the wafer volume.
Determining the production volume and mass, given the 26.8% volume increase due to processing.
5,252,034,808 mm3 * 126.8% = 6,659,580,137 mm3
Mass calculations given silica density of 0.00265g/mm3;
5,252,034,808 mm3 * 0.00265g/mm3 = 13,917,892 grams or 13,918 kilograms of Silicon in the wafers. 6,659,580,137 mm3 * 0.00265g/mm3 = 17,647,887 grams or 17,648 kilograms of Silicon required during production of the wafers.
Determining the amount of slurry waste during the wafer manufacturing process is a simple subtraction of the production mass and wafer mass;
17,648 kg - 13,918 kg = 3,730 kg of Silicon waste during wafer production
The purification method of the Silicon waste/slurry yields only 90% return rate. So of that waste 10% is lost, mass determined;
3,730 kg * 10% = 373 kg of Silicon is lost during wafer manufacture.
Between the manufacturing of the wafers and processing of the wafer into device/chips a combined "Recoverable" waste is given as follows;
3,357 kg (Wafer manufacturing) + 2,087 kg (Wafer Waste during production of devices) = 5,444 kg total Silicon waste in the production of iPhone 4/4S.
Potential Energy Savings[edit | edit source]
The energy savings in the recycling of Silicon during the manufacturing of iPhone components could be worth while. Calculations in the previous section, the 17,649 kg of Silicon material required to produce the silicon and 5,444 kg of recoverable material if required.
The amount of material that would be lost during the manufacturing of the devices would be calculated as;
5,444 kg / 17,648 kg = 0.308 * 100% = 30.8% of the total silicon used. So recovering this would seem to be very beneficial as 30%+ is a significant amount.
The energy (kW*hr) for one kilogram of Silicon during production will be 2933 kW*hr.[29] Taking the total wafer mass at 13,918 kilograms from the previous section, and the energy per kg and multiplying yeild;
13,918 kg * 2933(kW*hr/kg) = 40,821,494 kW*hr to produce the wafers.
Of the total energy, energy loss from the waste in the processing of the wafer to devices is calculated as;
2,087 kg * 2933(kW*hr/kg) = 6,121,171 kW*hr
The reclaiming of wafer waste during device manufacturing yields energy savings ranging from 50-90% <Will add Source>. For the sake of averages, averaging the range the recycling savings will be taken as 70%.
So of the device manufacturing processing an energy savings of 70% would save 4,284,819 kW*hr. For the amount of Silicon in the 3 components within total iPhone 4/4S units.
Energy savings for the production of the wafers for the amount of Silicon.
Reimplemantation Factors[edit | edit source]
Contamination[edit | edit source]
Sources:
- rogue chip material (partially processed chips)
- Inherent impurities in silicon (metallurgical grade vs chip grade silicon)
- Facility debris (waste water contamination / dust / fingerprints)
Characterization Methods[edit | edit source]
X-Ray Fluorescence spectroscopy is used to characterize the impurities in silicon crystals prior to being sliced into wafers. The usual impurities found are Phosphorus, Boron, Oxygen, and Carbon. Other elements sometimes found include Iron, Chromium, Nickel, Copper, Zinc, and Tin.[30]
Purification Process[edit | edit source]
The silicon that cannot be thrown directly back into the crusible and will need to be treated as metallurgical grade silicon. While there is not a cost savings due to processing, there is some monetary gain to be had for being able to reuse recyled material. A more anylitical study into how much money is saved is still under investigation.
Alternatives to "Classic" Recycling[edit | edit source]
Classic recycling involves processing products so that new products of equal or greater quality are produced. An example of this form of recycling is the recycling of paper. The final product has the same properties as the original paper, except now it can be written or printed on again, increasing the value of the paper. Classic recycling has limits though. If a product can be straight recycled at all, it is often a complicated process involving many dangerous chemicals. The cost of recycling is usually very high, sometimes even higher than collecting the new raw material. Also, products have a limited number of times it can be recycled before the integrity of the product is compromised.
In the case of this product which starts as high purity (electronics grade) silicon, the majority of the waste is during wafer production. This silicon does not see down-cycling into inferior products at all and is instead filtered, cleaned and re-melted back into the vat to grow more Si Crystal. Reclaiming silicon wafers outside of the wafer production is not uncommon and actually has a complete industry that takes device manufacturing waste (in the form of broken or non-usable wafers). This process waste is very valuable for other industries such as the manufacturing of PV devices like Poly-Silicon, which do not require as high of purity silicon.
Putting Together the Facility[edit | edit source]
In order to manufacture the components and recycle them the facility needs a location, some capital equipment, and a process flow map (outlined below).
Location[edit | edit source]
Ideally the facility would be a large enough facility that would produce both the Electronic Grade Silicon wafer and the finished product/product. Inside the facility the layout would allow the wafer manufacturing area to directly feed the other processes such as CMOS, CPU and NAND manufacturing lines. The recycling facility would have direct access to all four processing areas in order recollect the valuable semiconductor material and other process precious metals or materials.
Primary Capital Equipment[edit | edit source]
In order to run a successful operation considerations for capital equipment include but not limited to;
For during wafer production;
- Liquid/Wet Pump(s) for removal of the slurry produced -
- Processing Vats for slurry storage and processing -
- Slurry Filtration -
- Chemical Cleaning Bath -
- In-situ Analysis -
To reclaim broken, non-usable Silicon, to re-purpose through down-cycling;
- Surface Grinder -
- Flat Lapping Polisher -
- Chemical Vats/Baths -
Safety Plan[edit | edit source]
Within the recycling and manufacture facility constructed. The plant will follow all guidelines and regulations as defined by the Occupational Safety & Health Administration (OSHA) which if not followed would make the facility not able to operate should these guidelines not be followed. OSHA has defined regulations for Silicon device manufacturing. These regulations are found here.[31]
Employees of the recycling facility must be able to meet several requirements in order to be able to safely perform their duties, these include but are not limited to:
- Operation of high voltage equipment
Material Safety Data Sheets (MSDS)[edit | edit source]
In order to insure proper chemical and material handling, MSDS sheets are required to be used inside the facility with direct access to them by all employees.
The MSDS used in the recycling and manufacturing processes include:
- Sulfuric Acid (H2SO4)
- Hydrofluoric Acid (HF)
- Phosphoric Acid (H3PO4)
- Nitric Acid (HNO3)
- Ammonium Hydroxide (NH4OH)
- Hydrogen Peroxide (2(HO))
- Hydrochloric Acid (HCl)
- High Purity Water (H20)
- Trichlorosilane (SiHCl3)
- Phosphine(PH3)
- Lithium Aluminum Hydride(LiAlH4)
- Arsine (AsH3)
- Trichlorosilane (Cl3HSi)
Semiconductor Workflow[edit | edit source]
Considering the ideal location and area where a plant could be put down and that it would want to encompass both the wafer and device production. A possible Work Flow diagram is given below;
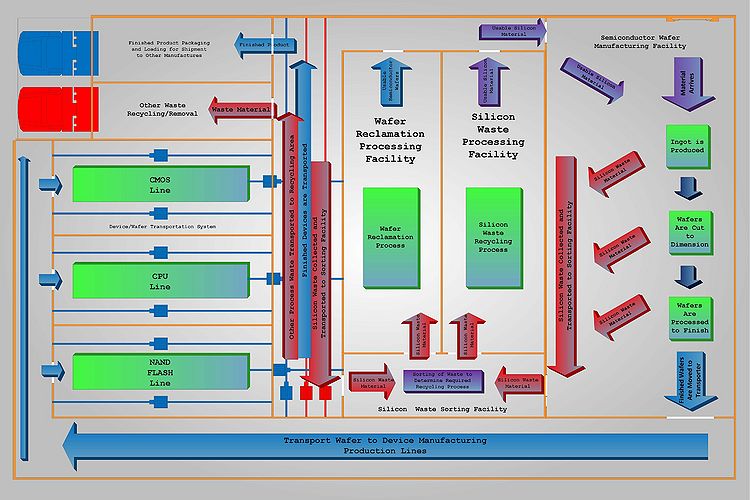
References[edit | edit source]
- ↑ Walter Galan, iFixIt. iPhone 4S Teardown
- ↑ Apple, Inc. Apple Press Release - 2010 Q3
- ↑ Sinead Carew, Reuters. Apple Sells 1.7 million iPhone 4
- ↑ Apple, Inc. Apple Press Release - 2010 Q4
- ↑ Apple, Inc. Apple Press Release - 2011 Q1
- ↑ Apple, Inc. Apple Press Release - 2011 Q2
- ↑ Apple, Inc. Apple Press Release - 2011 Q3
- ↑ 8.0 8.1 Apple, Inc. Apple Press Release - 2011 Q4
- ↑ 9.0 9.1 Apple, Inc. Apple Press Realease - iPhone 4S Sales First Weekend
- ↑ Apple, Inc. Apple Press Release - 2012 Q1
- ↑ Apple, Inc. Apple Press Release - 2012 Q2
- ↑ Apple, Inc. Apple Press Release - 2012 Q3
- ↑ Richard Goodman. iPhone 4S Sales to Remain Strong
- ↑ Jonathan Ratner. UBS Cuts iPhone Shipment Forecast
- ↑ Apple, Inc. Apple Recycling Program
- ↑ PowerON Homepage
- ↑ 17.0 17.1 WeRecycle! Homepage
- ↑ Abhay Paliwal, Impact of Tablets and Smart Phones on Semiconductor Component Demand
- ↑ Kevin Keller, iSupply iPhone 4 Bill of Materials
- ↑ Andrew Rassweiler, iSuppli iPhone 4S Bill of Materials
- ↑ How Integrated Circuits are Made
- ↑ Size of A5 microprocessor
- ↑ OnmiVision Technologies, Inc., OV8830 8mp CMOS Image Sensor
- ↑ Dr. Helmut Föll.,"Materials and Processes For Silicon Technology". University of Kiel, Materials Institute, 2007.
- ↑ Endress+Hauser
- ↑ Dr. Helmut Föll.,"Silicon Process Flow Digram", University of Kiel, Materials Institute, 2008.
- ↑ Reinhardt, Karen.,"Cleaning for Semiconductor Manufacturing", Wiley and Sons.
- ↑ Molly Riddell.,"Shining A New Light on Silicon PV Manufacturing", Continuum Magazine, National Renewable Energy Lab (NREL.gov), Issue 3.
- ↑ E.D. Williams, R.U. Ayres, M. Heller The 1.7 Kilogram Microchip Environmental Science and Technology, vol. 36, no.24, 2002, pp.5504-5510.
- ↑ it.science.cmu.ac.th/ejournal/dl.php?journal_id=432
- ↑ Occupational Safety & Health Administration.,"Silicon Device Manufacturing".
- ↑ E.D. Williams,"Environmental Impacts of Microchip Manufacture," Thin Solid Films, vol. 461,no. 1, 2004, pp.2-6.