Cadmium Telluride (CdTe) photovoltaic modules consist of five primary layers. These layers, especially the CdTe layer, are applied using a variety of deposition methods. Figure 1 depicts a basic flow diagram for the steps to produce these solar cells.

Further details of each layer, the deposition method used and equipment involved are described below.
In order to produce these modules at production volumes, many manufactures are beginning to rely on automated single stream in-line manufacturing cells.[1] Total manufacturing costs for a new manufacturing facility and all capital equipment is estimated at $1.50/watt with manufacturing costs below $1.00/watt.[2]
Front Glass[edit | edit source]
The substrate consists of a 3mm thick layer of soda-lime glass. Soda-lime glass is used as an alternative to more expensive materials, such as borosilicate glass.[1] The glass enters the first manufacturing cell where it is washed and placed under vacuum. The module will remain under vacuum for the duration of the manufacturing process.[2]
Transparent Conducting Oxide (TCO)[edit | edit source]
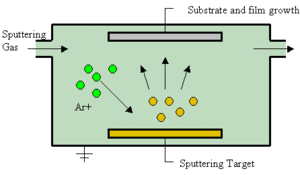
In the next cell the transparent conducting oxide is applied, consisting of tin-doped indium-oxide(ITO). The ITO layer is 500 nm thick and is applied via a physical vapor deposition method called sputtering.[1] Sputtering deposition consists of high energy particles directed at a target (in this case, ITO) to remove particles and deposit them on a substrate (soda-lime glass). An inert gas, typically argon, is present in the sputtering chamber as seen in Figure 2. Increasing the pressure of the inert gas causes the target atoms to move diffusively and can help control the motion and impact of the target on to the substrate.[3] The entire sputtering process for the TCO layer takes approximately 5-10 minutes to complete.[1]
CdS[edit | edit source]

A 100 nm layer is applied on top of the TCO by a method called close-spaced sublimation (CSS). A diagram of CSS is outlined in Figure 3. A stainless steel chamber is pressurized to a maximum pressure of 400 torr with an inert gas, typically argon. The source and substrate are separated by a distance of 2-6 mm and the chamber is elevated to a temperature of approximately 1800°C (the melting temperature for CdS is approximately 1750°C), while the substrate stays at an operating temperature of 500°. The argon atmosphere encourages higher deposition rates. Oxygen is also introduced during sublimation. The oxygen is believed to decrease the CdS grain size & improve efficiencies; however, it also lowers the deposition rate.[1][4]
CdTe[edit | edit source]
Following the coating of CdS, a thin film of CdTe is then deposited on to the substrate. The cadmium and tellurium elements used in this layer can be obtained as byproducts from zinc and copper refining.[5] Close-spaced-sublimation(CSS) or electrodeposition may be used to apply the 8 µm thick film.[1] The substrate is maintained at 500°C, while the oven is heated above the melting temperature of CdTe, to 1200°C. The chamber is pressurized with an inert gas under similar processing conditions as the CdS layer. The total deposition time is approximately 2 minutes, deposited at a rate of 4µm per minute.[1]
Chlorine Treatment[edit | edit source]
Treating the cadmium layers with chlorine is an important step in the manufacturing process. The addition of chlorine increases the size of small grains in the microstructure. Larger grain sizes help the crystalline structure of the CdTe and hinder the formation of an inter-diffused layer at the CdS and CdTe border; both significant factors in improving cell efficiency. Chlorine is applied by evaporation of CdCl2. The surface is then etched in a Br-methanol solution to remove any oxidation that occurs during treatment, providing a clean surface for the back contact.[1][4]
Back Contact[edit | edit source]
The back contact can be created using several different materials. Copper gold, and copper graphite combinations have been used for the back contacts, but the efficiency of these materials limits the ability of the CdTe due to the diffusion of copper into the superstratum. Sb2Te3 and As2Te3 are two materials that can be sputtered on the unblemished surface of a CdTe semiconductor. The back contact should be processed at 300°C (Sb2Te3), and 250°C (As2Te3); layered at a thickness of approximately 150nm.[1]Sb2Te3 and As2Te3 both form p-type semiconductors with resistivities of 10-3 and 10-4 ohms respectively. The final step in forming this back contact consists of a (150nm) coating of molybdenum.
Raw Material Utilization and Waste for Thin Films[edit | edit source]
The most common current processes for applying these thin films are variants of sputtering and sublimation, despite the fact that they tend to be less efficient in terms of material utilization. Anywhere from 30% to 70% of the sputtering target material may be deposited on the chamber walls where it is difficult to extract in a form pure enough to reuse. Close-spaced sublimation is reported to waste approximately 50% of the material in deposition. Newer techniques in testing, such as electrodeposition, have been shown to have material utilization rates up to 95%,[6] which would offer a considerable savings in the cost of the more expensive raw materials. As an example, two methods of CdTe thin-film deposition are shown in the table for comparison.
Material | Deposition Method | Est. Deposition Efficiency | Film Thickness, (μm) | Film Density, (g/cm3) | Film Mass (g/m2) |
Material Consumed (g) |
Material Cost (USD/g) |
Material Cost (USD/m2) |
Material Cost (USD/Wp) |
Deposition Waste (g/m2) |
Deposition Waste (mg/Wp) |
---|---|---|---|---|---|---|---|---|---|---|---|
CdTe | CSS | 75%[6] | rowspan=2 | 6.2[7] | 24.8 | 34 | 0.17[6]|6 | 0.076 | 9.6 | 120 | ||
Electrodeposition | 2 | 12.4 | 13 | 2.20 | 0.028 | 0.65 | 8.42 | ||||
CdS | 50% | 0.1 | 0.48 | 1.0 | 0.35[9] | 0.34 | 0.0043 | 0.50 | 6.4 | ||
CdCl2 | Evaporation | 75% | 0.1 | 0.48 | 0.54 | 0.43 | 0.0056 | 0.14 | 1.74 | ||
Sn-Doped In2O3 | Sputtering | 50% | 0.5 | 0.41 | 0.54 | 13 | 0.16 | 1.20 | 15.5 | ||
Sb2Te3 | Sputtering | 50% | 0.15 | 0.97 | 1.3 | 2.16[10] | 2.80 | 0.04 | 0.32 | 4.15 |
These material prices are quoted from a few common suppliers for high-purity chemicals. With the process at full scale, the materials cost would be significantly reduced. Thickness of each layer of a CdTe panel varies depending on the process, but the values shown are close to average from published sources. The mass, per m2 panel, of each layer was simply calculated from the typical film thickness and material density, and divided by approximate material utilization efficiency as shown in the following equations.
(1)
(2)
(3)
It is assumed that one m2 CdTe panel has a peak power output of about 80 W,[11] which is typical of CdTe panels after some degradation that begins to occur immediately after installation. The cost per watt of peak power output (Wp) was calculated from equation 4.
(4)
The amount of waste is simply the difference between the amount of material deposited in the panel and the amount of material consumed, which is divided by the peak power to calculate the amount of waste per Wp.
(5)
(6)
The best solution for eliminating waste during these processes is to increase the efficiency of the machine. This can not always be performed. The processes for recycling this material are outlined in the separation and recovery section below.
CdTe Production Waste Recovery and Separation[edit | edit source]
- Please Note all Math Type Equations are corrected work and could not be modified to be RED. Thank You.
During deposition of CdTe in the CSS process, the CdTe gas will solidfy on the graphite walls which surround the glass substrate. This solidification on the walls leads to the decrease in utilized CdTe. At set intervals, the graphite walls are cleaned and the CdTe must be purified to be reused within this process. Collected CdTe can be reclaimed and purified through a process consisting of: hydrometallurgy, ion exchange, and electowinning.
The CdTe reclaim process begins with the leaching of the solidified mixture of CdTe, graphite, and additional impurities added within transport to the reclaim center. A mixture of sulfuric acid (approximately 478 ml/kg-mixture) and hydrogen peroxide (approximately 12.8 ml/kg-mixture) is used to separate the contaminates,.[12] Typical leaching time to obtain complete extraction of CdTe is 120 minutes. The Cd and Te are then separated by ion-exchange, which yields a separation efficiency of 99.99% or higher. After the ion exchange process, cadmium is recovered by electrowinning while tellurium is recovered by precipitation using sodium carbonate and sodium sulfide. After these processes, the cadmium and tellurium can be further purified using vacuum distillation techniques explained below,.[12]
To estimate the amount of energy required to separate a specific mass of waste CdTe in a 1GW recycling facility, the total amount of waste and process equipment energy were determined.
Calculation of Total Modules in 1 GW of PV Production[edit | edit source]
Where is the total energy produced by all modules built in one year, is the energy output of one module and is the number of modules.
Therefore:
Calculation of Total Surface Area in 1 GW of PV Production[edit | edit source]
Where is the number of modules produced, is the length of the module, is the width of the module, and is the total area of all modules.
Therefore:
Mass of Daily Waste CdTe produced in 1GW PV Modules[edit | edit source]
Assuming the facility works 360 days in one year, the mass of CdTe to be separated daily would be 248 kg. Analysis of this rate is shown below.
Where for CSS of CdTe in table above, is the utilization rate in table above, is the waste CdTe per day, and is the number of working days in one year.
Therefore:
Specific Energy of Separation[edit | edit source]
During the stated separation regime three different processes are addressed: Hydrometallurgy, Ion Exchange, and Electowinning. In all three processes, appropriate industrial equipment was identified. Each machine was determined to be run contiunously within the 360 day working year.
During the hydrometallurgy or leaching process, sulfuric acid and hydrogen peroxide are pumped around the waste CdTe. Within this process, the only power requirement is the pump which continously pumps the solution around the waste and to the next part of the process. The power required by a by a typical 12 V transfer pump is determined below.
Where is the power required by the pump, is the current drawn from the pump, and is the voltage required from the pump.
.[13]
.[13]
During the ion-exchange process to separate Cd, a U.S. Filter UHP-10 ion exhange module was run continuously. The power required by this module is calculated below.
Where is the power required by the ion-exchange module, is the current drawn from the ion-exchange module, and is the voltage required from the ion-exchange module.
*
.[14]
- Note 20 Amp service is assumed for a typical 120 V outlet
The specific power consumption of hydrometallurgy and ion exchange is shown below using the known power required by each piece of equipment and the rate of waste CdTd production.
During the recovery of tellurium, it is precipitated out using sodium carbonate and sodium sulfide. Through this process, an electric tranfer pump is used to move all the liquids. The power required by a by a typical 12 V transfer pump is determined below.
Where is the power required by the pump, is the current drawn from the pump, and is the voltage required from the pump.
.[13]
.[13]
The specific power consumption of hydrometallurgy and ion exchange is shown below using the known power required by each piece of equipment and the rate of waste CdTd production.
Within the electrowinning process to capture Cd, a Remco Engineering electrowinning unit was considered. A known specific power was given for the electrowinning process as shown below and the overall energy of all three processes is shown below.
.[15]
Adding all the specific energies of separation:
CSS Waste Recycling Flow Chart[edit | edit source]
Because of the impurities post Cation Exchange, the Cd and Te must then be sent through a vacuum distillation process (outlined below).
Cd and Te Purification and Characterization Techniques[edit | edit source]
To produce solar grade Cd, 99.999% purity[16][17] is required while semiconductor Cd grades require purity levels of 99.9999%.[16] To obtain solar grade Cd, metallurgical grade Cd (99.99% purity) is further processed through vacuum distillation. Within vacuum distillation, the metallurgical grade Cd is heated in a crucible under a vacuum and melts the material. When the melting temperature of an impurity element is achieved and the vapor pressure of the impurity is higher than the impurity of the element in the gaseous phase, the impurity evaporates and condenses within a cooled collector. Purification efficiency is within the range of 80 to 90 % and depends on the evaporation rate of substance, transportation of vapor, vacuum pump capacity, crucible material, and heating and cooling methods.[18] Purification of semiconductor grade Cd requires zone refining and efficiencies of 94.6% may be achieved with up to 25 intervals.[19] To assess the degree of purification atomic absorption spectroscopy, spark source spectroscopy, laser scan mass spectroscopy, glow discharge mass spectroscopy, inductively coupled plasma mass spectroscopy, and inductively coupled plasma optical emission spectroscopy may be used.[18] Atomic absorption spectroscopy can be used to determine, in an in situ fashion, the purity of the consumable Cd. The energy used during purification of Cd using a Wastech Model Sigma DT 300 Vacuum Distillation System (VDS) was calculated to be 5.619 * 10-6 kWh/g as shown in equation 14.
(14)
[20] * Assume RMS Value
Tellurium used in production of solar cells requires 5N5 or 99.9995% purity and higher grades for semiconductor materials.[22] To obtain solar grade purities, single run multiple vacuum distillations are performed. Multiple zone refining techniques are additionally used to achieve semiconductor grade Te.[23] An overall efficiency of 95.5% is achieved during the purification of 5N5 Te. Tellurium purity can be characterized by x-ray diffraction techniques and with a inductively coupled plasma emission spectrophotometer are employed.[24] X-ray diffraction can be used within the manufacturing process for automated process control. The energy used during purification of Te using a Wastech Model Sigma DT 300 Vacuum Distillation System (VDS) was calculated to be approximately 7.7897 * 10-6 kWh / g as shown in equation 15.
(14)
[20] * Assume RMS Value
In situ monitoring of the Cd and Te during the manufacturing process may be done with spectroscopic ellipsometry and optical monitoring. Spectroscopic ellipsometry is a process in which a light beam is reflected off the sample of interest and changes in the light beam are assessed to determine properties including: composition, film thickness, refractive index, surface roughness, interfacial regions, anisotropy, crystallinity, and uniformity.[25] Within spectroscopic ellipsometry, models of ideal and non-ideal cases can developed to create in process control systems which will allow a completely automated system which is non-destructive,.[26]Within the CSS deposition system, optical monitoring of the partial pressures of Cd and Te may be correlated with purification standards and compositional changes.[27] Within optical monitoring, a laser source is directed at the material and the absorption of the material is function of the purity. Small derivations from the sublimation compostion result in large increases in vapor pressure.[27]
Module Waste Separation and Recovery Processes[edit | edit source]
Full CdTe photovoltaic modules as well as manufacturing waste material collected from the deposition methods described above can be recycled into several reusable byproducts with four pieces of common industrial equipment. First electrical bus connectors are removed manually. The modules and manufacturing waste are reduced in a hammer mill and particles between 6 and 60 mesh consisting of glass and film layers are removed. Particles above this size, still within the hammer mill and consisting of elastomeric mounting feet and electrical potting, are collected.
The recovered glass and film layers enter a rotating conical barrel finishing machine filled with sulfuric acid and hydrogen peroxide. The chemical reaction within of this process is shown in equations 7 and 8. Typically this reaction can remove 30 to 40 g/L of CdTe or 1 liter of etchant can be used on two photovoltaic modules. Left over glass and ethylene-vinyl acetate are rinsed and smaller glass particles are screened and collected for salable glass cullet,.[28]
CdTe +3H2SO4 +3H2O2 = CdSO4 + Te(SO4)2 +6 H20 (7)
CdS+H2SO4+H2O2=CdSO4+2H2O+S(8)
The metals are coprecipitated out using Na2SO2 and a sludge press.[28]Sludge resulting from this process is allowed to settle and then pressed. Effluent of the sludge press is treated with ion exchange to reduce cadmium levels to non-detectable levels. The principle reactions used in this recovery of Cd and and Te are shown in equations 9 and 10.
CdSO4 +Na2CO3 = CdCO3 + Na2SO4(9)
Te(SO4)2 +2Na2CO3 = TeO2 +2Na2SO4 +CO2(10)
The sludge cake can then be used by a CdTe manufacturer to regenerate CdTe with a hydrogen furnace with reactions in 11 and 12.[28]
CdCO3 +TeO2+3H2=Cd0 +Te0+CO2+3H2O(11)
Cd0 +Te0 = CdTe (in N2 at 500o C})(12)
The collection method described above uses 7.77 x 10-5 kW-hr/g of recovered material. These calculations are based on the mass of the entire photovoltaic unit. Calculation is shown in Eq. 13.
(1KW-hr/ Cost of Electicity) * (Energy Cost of Recycling/ Watt of PV module) * (Watt / PV module) * (PV Module/ Weight of Module) * Weight to Mass Conversion = Energy Used/ Mass Material Produced(13)
Cost of Electricity = $0.12[29]
Energy Cost of Recycling / Watt of PV module = $0.0023/Watt,.[28]
Watt / PV module = 50 W / Unit,.[28]
Weight of Module = 27 lb /module[30]
Weight to Mass Conversion = 456.6 g / lb.[30]
The collection efficiencies of this process include:
- 98% of the glass is recovered with losses associated to dust collection system.
- 95% of the Ethylene –vinyl acetate is recovered with some losses when potting is discharged.
- 99% Cadmium and Tellurium is recovered in sludge process
During the collection of CdTe sludge impurities such as the back metal contact may be found within the media. This accounts for less than 1% of the mass of the sludge. Reclaimed glass may contain sulfur less than 20 ppm and is still salable at this contaminate level.[28]
Module Recycling Process Flowchart[edit | edit source]
The Process for recycling the semiconductor involves little human interaction. The initial process of removing components that cannot be machine controlled require handling. Once the components are crushed, they are moved through the process by machine. Energies and yield can be viewed in the section above CdTe Waste separation and Recovery Processes.
Plant Down cycling and Development Ideas[edit | edit source]
Distances from the recycling facility are shown in parentheses after the name of each prospective customer.
Polyurethane mounting feet and electrical potting are removed from the hammer mill after the crushing process is completed. The crushed glass and semiconductor (CdTe film and ethylene vinyl-acetate) is transported by conveyor for further breakdown and processing. The other components are removed and sent to a non-hazardous waste area, where they will be manually sorted and prepared for shipping. insert reference Plastic components will be sent to Ohio Polymers Recycling INC. (127) miles from the recycling facility. Electrical wire is shipped to Omni Source (2.3 mi) for recycling. Electrical wire comes as a profit since it can be sold as #2 copper. Waste glass from the recycling process will be washed to remove any residual semiconductor particles, and shipped to Libbey Glass (7 mi)for uses in. The downside of shipping the plastics to Ohio Polymers is that it is the greatest distance away out of all of the byproducts formed. On a positive note, they will take every scrap polymer used in the process, and recycle it accordingly.
Cadmium can be sold to Crown Battery (42.7 mi) for the manufacturing of Nickel Cadmium batteries. Another possible use of cadmium is for neutron absorption in a nuclear reactor.[31] There is a nuclear power plant being developed in Newport Michigan (23 mi), and will have use for the cadmium in their control rods.
Tellurium is added to steel to increase its machining capability.[32] Companies such as Northstar Bluescope steel (32.7 mi), Great Lakes Steel (47.6 mi) and Severstal (50 mi) would purchase the raw tellurium after it is separated from the sludge cake.
Since the layer of cadmium telluride is very small on these devices, the acquisition of substantial amounts will take a lot of time.
CdTe Uses – A hydrogen furnace would reduce the sludge cake to Cadmium, Tellurium, Carbon dioxide, and water. The recycling plant would have a multiple Bridgman furnaces for the recombination of cadmium and tellurium to form CdTe. The process would involve heating the cadmium telluride in the furnace to promote vertical crystal growth. Electrical and photoluminescence would be used in-situ do determine the purity of the CdTe crystal[33]. The finished product can then be sold to First Solar (14.5 mi) for the reformation of semi-conductors, or to a facility for creation of nuclear radiation detection devices. This provides the recycling facility with an advantage over first solar's CdTe suppliers because of its distance from the plant. Unfortunately, the formation of CdTe at the recycling facility requires extra energy, which in turn costs more.
Students from the physics department in the University of Toledo (7 mi) would be drawn to our facility as an opportunity for work experience. We would continually have at least 2 co-op students and 1 summer intern in our facility at all times. This provides the recycling facility with individuals with a technical background at a low cost.
There are several advantages of having a full process recycling facility in Toledo. Each semiconductor component is fully recycled, and there is little that actually goes to waste. Most of the companies that take the recycled components are very close to the recycling facility. This promotes economic and environmental sustainability. Several jobs will have also been created. The processing of these materials remains in the state, and does not get outsourced. The use of semiconductors is greatly increasing as renewable power sources are being sought after, which provides an increase in business as time goes on. There are a few disadvantages that inhibit the growth of the company. Due to the small amount of CdTe actually used in these panels, a lot of spent semiconductors are needed to obtain a usable amount. Panels usually last for 20 years before recycling is even needed. The rate at which these semiconductors decay can create speed bumps in continuous recycling. Advancements in technology could eventually forever change how these materials are made, and could drastically sway the way the recycling business is run.
Safety Plan[edit | edit source]
The Occupational Safety and Health Administration (OSHA) is an organization with the United States Department of Labor whose mission is to:
…ensure safe and healthful working conditions for working men and women by setting and enforcing standards and by providing training, outreach, education and assistance.[34]
The recycling facility described above will follow all OSHA requirements including, but not limited to, those listed below. More information on OSHA regulations can be found on their website at http://www.osha.gov/.
Material Safety Data Sheets (MSDS)[edit | edit source]
Material Safety Data Sheets are required for all chemicals that enter the plant. MSDS's will be located in areas where the materials are stored and used in a manner that they are accessible to all employees. A list of the primary materials used in the recycling process, along with links to their MSDS, can be found below.
Recovered Solar Module Materials
- Cadmium Telluride [CdTe MSDS]
- Cadmium Sulfide CdS MSDS
- Soda-Lime GlassSoda-Lime Glass MSDS
- Indium-Tin Oxide[Tin doped In2O3 MSDS]
Materials used in recycling process
- Antimony TellurideSb2Te3 MSDS[35]
- Arsenic TellurideAs2Te3 MSDS[35]
- Sulfuric Acid[H2SO4 MSDS]
- Hydrogen Peroxide[H2O2 MSDS]
- Ethylene-vinyl acetate (EVA)EVA MSDS
- Sodium Sulfate[Na2SO4 MSDS]
- Sodium Carbonate[Na2CO3 MSDS]
Safety Training & Communication Program[edit | edit source]
The recycling facility will provide a Safety Training and Communication Program. The purpose of this program will be to train new employees, communicate current and long-term safety issues to all employees as well as evaluate and update procedures on various topics. Some areas the Safety Training and Communication Program will focus on include:
- Wearing Proper PPE
- How to read a MSDS
- Emergency Response: Hazardous Chemicals
- Review of Hazardous Chemicals
- How to prevent/clean-up spills
- How to properly label containers
- Procedures for handling chemicals
Chemical Storage and Handling[edit | edit source]
All chemicals within the plant must be stored in approved containers and located in cool, dry, well-ventilated areas. Hydrogen Peroxide must be stored in a separate location from other materials because it is an oxidizer. Safety goggles, gloves and respirators (when in powder form) must be worn in all work and storage areas. In addition, a full impervious suit, boots and face shield must be worn when near Sulfuric Acid, Sodium Carbonate and Sodium Sulfate. All spills should be cleaned up quickly according to the MSDS and OSHA guidelines. Workstations should remain clean and orderly per company 5S standards in order to help minimize employee errors and increase safety.
OSHA defined Permissible Exposure Limits (PEL) apply to the following materials:
- CdTe 0.005 mg/m3 (Cd)
- CdS 0.005 mg/m3 (Cd)
- Sb2Te3 0.1 mg/m3 (Te)
- Ab2Te3 0.01 mg/m3 (As)
- H2SO4 1 mg/m3
As in most industries, fire hazards are present and must be taken seriously. The local fire department will be invited to visit the recycling facility prior to the start of manufacturing in order to become familiar with the building. The fire system will also be checked on a monthly basis to ensure it is working properly. Multiple chemicals used in the facility can emit toxic fumes during combustion, including: CdS, Sb2Te3, Ab2Te3 and EVA. Proper ventilation must be present in all chemical work and storage areas. H2O2 must be stored independently of other chemicals since it is an oxidizing material and presents a greater fire risk. Acids, such as Sulfuric Acid will also be stored separately due to their corrosive nature. All chemicals will be stored in fireproof storage cabinets that are labeled according to OSHA standards. Fire extinguishers will be located near the cabinets. Each chemical's MSDS will list the appropriate type of fire extinguisher necessary. Fire extinguishers will also be located throughout the plant at strategic locations.
Possible Plant Floor Plan[edit | edit source]
This is a possible floor plan design for the recycling facility. Office and chem lab placement was chosen based on an area of the plant where sorting and processing is not occurring. The only flaw in having an office placed here is the vibration and noise from the hammer mills. The office and chemlab space would need to be created so that these factors are reduced to a minimum.
Team Members[edit | edit source]
References[edit | edit source]
- ↑ 1.0 1.1 1.2 1.3 1.4 1.5 1.6 1.7 1.8 Romeo N. et al High Efficiency CdTe/CdS Thin Film solar Cells by a Process Suitable for Large Scale Production
- ↑ 2.0 2.1 Barth K. Abound Solar's CdTe Module Manufacturing and Product Introduction
- ↑ http://en.wikipedia.org/wiki/Sputter_deposition
- ↑ 4.0 4.1 Ferekides C. et. al., The Effects of CdS Processing and Glass Substrates on the Performance of CdTe Solar Cells
- ↑ Meyers P., First Solar Polycrystalline CdTe Thin Film PV
- ↑ 6.0 6.1 6.2 6.3 6.4 Ken Zweibel, Thin film PV manufacturing: Materials costs and their optimization, Solar Energy Materials and Solar Cells, Volume 63, Issue 4, 31 August 2000, Pages 375-386, ISSN 0927-0248, 10.1016/S0927-0248(00)00057-X. (http://www.sciencedirect.com/science/article/pii/S092702480000057X)
- ↑ 7.0 7.1 7.2 7.3 7.4 http://www.matweb.com/
- ↑ 8.0 8.1 8.2 8.3 Bohland J. Economic Recycling of CdTe photovoltaic Modules
- ↑ 9.0 9.1 9.2 http://www.sigmaaldrich.com/
- ↑ http://www.lesker.com/
- ↑ www.nrel.gov/docs/fy06osti/38938.pdf
- ↑ 12.0 12.1 Fthenakis V. and W.Wang. Extraction and separation of Cd and Te from Cadmium Telluride Photovoltaic Manufacturing Scrap.
- ↑ 13.0 13.1 13.2 13.3 Commercial Fuel Solutions 12V Fuel Pump
- ↑ U.S. Filter www.ebay.com/itm/U-S-Filter-UHP-10-Ion-Exchanger-DI1013-/160493065169
- ↑ www.remco.com
- ↑ 16.0 16.1 Fthenakis, Vasilis. Environmental Life Cycle assessment of cadmium telluride solar cells: Cd Emissons.
- ↑ Fthenakis, Vasilis. Hyung Kim. Erik Alsema. Emissions from Photovoltaic Life Cycles.
- ↑ 18.0 18.1 Ali,S. et al. Purification of Cadmium to 5N+ by vacuum distillation.
- ↑ Ali,S. et al. A novel in-situ technique of ultra purification of cadmium for electronic applications.
- ↑ 20.0 20.1 20.2 20.3 20.4 20.5 http://web.archive.org/web/20150502183149/http://www.wastechengineering.com:80/products/vacuum-distillation-systems.html.
- ↑ 21.0 21.1 https://www.wolframalpha.com
- ↑ Ali,S. et al. Purification of tellurium by single-run multiple vacuum distillation technique.
- ↑ Ali,S. et al. Purification of tellurium by single-run multiple vacuum distillation technique.
- ↑ Munirathnam, Et al. Purification of tellurium to 6N+ by quadruple zone refining.
- ↑ Tomkins, Harland. Spectroscopic Ellipsometry. https://www.aps.org/units/fiap/meetings/presentations/upload/tompkins.pdf
- ↑ Almeida, L. Automated Compositional Control of HgCdTe During MBE, Using in situ spectroscopic ellipsometery.
- ↑ 27.0 27.1 Zappettini, A. F. Bissoli. Optical Monitoring of Partial Vapor Pressures in CdTe and CdZnTe Systems: A New Tool for Material Technology Development.
- ↑ 28.0 28.1 28.2 28.3 28.4 28.5 Bohland J. Economic Recycling of CdTe photovoltaic Modules
- ↑ Funk, John. The Illuminating Co., Ohio Edison and Toledo Edison to pay less for power beginning in May
- ↑ 30.0 30.1 Wohlmuth W. Thin Film CdTe Module Manufacturing.
- ↑ Cruetz, Edward C. and Zinn, Walter H. "Neutronic Reactor Control" Patent 2,781,308. Feb. 12, 1957
- ↑ 2Kosa, Ted, and Ronald P. Sr. Ney. "Machining of Stainless Steels." ASM Handbooks Online. ASM International, 2002. Web. 5 Oct 2011. <http://products.asminternational.org/hbk/index.jsp>.
- ↑ Triboulet, R, Y Marfaing, A Cornet, and P Siffert. "Undoped high-resistivity cadmium telluride for nuclear radiation detectors." Journal of Applied Physics. 45.6 (1974): 1-7. Web. 5 Oct. 2011. <http://scitation.aip.org/getpdf/servlet/GetPDFServlet?filetype=pdf&id=JAPIAU000045000006002759000001&idtype=cvips&doi=10.1063/1.1663661&pr
- ↑ www.osha.gov
- ↑ 35.0 35.1 http://www.espimetals.com/index.php/msds