In Sri Lanka, home composting is promoted in many municipalities as a simple and low-cost solution to emerging waste disposal problems in the present day society. In this process, valuable compost is produced using the organic components of household waste that we dispose of as being spent, useless, worthless, or in excess to our needs.
Different types of home composting units/bins are available in the market, which are manufactured from plastic, metal or concrete rings. Concrete bins have been identified as the most cost-effective and environmentally friendly solution, when compared to other designs. Production of concrete bins has been limited to a few fabricators in the capital city Colombo but there is a huge gap in the dissemination of this knowledge to the other small-scale fabricators in other parts of Sri Lanka. Therefore, this technical brief is intended to disseminate the technology of concrete composting bin fabrication.
Main component of 3-ring concrete compost bin
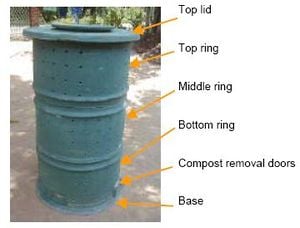
Moulds for the manufacturing process[edit | edit source]
During the bin fabricating process, each component of the bin is moulded separately in concrete. Moulds can be prepared using metal sheets or, preferably, fibreglass. Separate moulds are required for:
- Basement
- Bottom ring
- Middle ring
- Top ring
- Top cover
- Covering lid
- Compost removing doors
Materials required for fabrication one concrete bin
Description | Amount/rate | Cost (Rs) as prices on 1/06/2005 |
---|---|---|
Cement (rapid hardening cement | 30.0 kg (cost-18000.00/mould) | 300 |
Iron (1/4" rods) | 1.25 Kg | 112.50 |
Metals (3/4") | 1.5 cu ft | 60.00 |
Sand | 1.25 cu ft | 50.00 |
Paints | 3 bins/person/day | 60.00 |
Labour | Assuming 100 bins are produced from 1 mould | 275.00 |
Cost for mould | 180.00 | |
Total | 1037.50 |
Fabrictaiong Process
A) Preparation of the concrete mixture
Material | Ratios |
---|---|
Sand | 4 pans (screened through 1/2" mesh) |
Metal | 3 pans (size 3/4") |
Cement | 30 Kg |
Materials above should be well mixed and then gradually add water to have a free-flowing concrete mixture. A good finish can be expected by adding 1 pan of quarry dust.
B) Bottom pad
Steps:
- Get the bottom pad mould (1" width iron ring that is bolted by one side) and place it on a polythene sheet laid on levelled ground (Plate-02).
- Pour concrete mixture into the mould (half –fill).
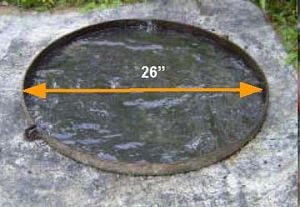
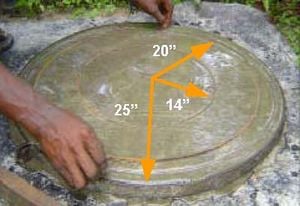
- Place iron rings (¼") as in diagram (three rings) Plate-03.
- Fill the mould with concrete mixture covering the iron rings completely.
- Level the surface using a straight pole and remove the excess concrete from the mould (maintain thickness 1").
- Locate 4-5 PVC pipe pieces (½ " diameter and 2" long each) to make the pad porous (Plate -04).
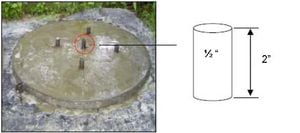
C) Bottom, middle and top rings (depend on the design)
- Get three separate moulds for top middle and bottom rings (correctly fix all components of each mould using bolt and nuts).
Before fixing the ring parts of the mould, some burnt oil (oil from petrol vehicles is preferable) can be applied to the inner side of the mould. It makes it easier to remove the blocks form the mould.
- Locate the moulds on levelled ground (Plate 05 and 06).

- Get the concrete mixture and pour it in to the moulds to fill 1-1.5" from the bottom (Plate -07).
- Insert first iron ring between inner and outer moulds – should not touch the walls of the moulds
- Fixed the plugs for aeration holes in all bins (Plate-09)
- Add concrete mixture gradually and spread it uniformly with a stick (Plate -08)
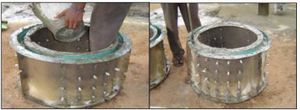
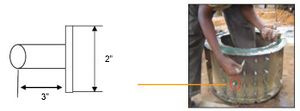
For middle and top rings
- Once the mould is filled up to 1-1.5" from the top level-place 2nd iron ring as first ring (Plate10).
- Fill the concrete mixture up to the top level of the moulds and levelled using a trowel
- After 30 minutes, fix the strip to the mould and add some mortar to make the inner interlocking grove (only for middle ring) and levelled (Plate-11).
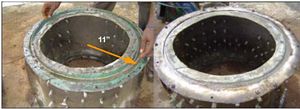
For bottom ring
- Stop the filling the mould once the level of the concrete is close to 4" form the top.
- Insert the 2nd iron ring and add 1" thick concrete layer on it.
- Insert 3 sockets with equal spacing to leave the space for compost removing doors (Plate-12).
10. Fill the space between the sockets and insert iron rods from the sides of each door (6 rods 15" long and ¼" diameter) (Plate-13).
11. Cover the iron rods level the surface.
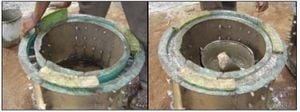
c) Top cover
- Place the mould on levelled ground.
- Apply some oil inside the mould (Plate -14)
- Fill the mould with concrete (¾ " from bottom).
- Place two iron rings (¼") (Plate-15).
- Fill with concrete up to the top level of the mould (1.5") leaving the space for the door (Plate-16).
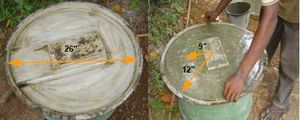
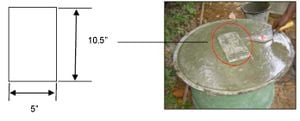
d) Top lid and compost removing doors
- Place the mould on levelled ground.
- Apply some used oil in side the mould (Plate-17).
- Fill the mould with concrete (half).
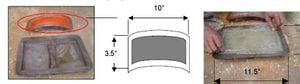
- Place iron rods as shown in the diagrams (Plate-18).
- Fill with concrete up to the top level of the mould and levelled well.
e) Remove the moulds
If rapid hardening cement was used, the mould can be removed after 24 hours. Special care should be taken to remove the moulds from the concrete rings. Inner mould should remove first to minimise possible damage.
- Remove bolts and nuts in the flange of the inner mould and loosen it from the mould with a little knocking (Plate-19).
- Remove the inner mould with little curling (slide upwards) (Plate-20).
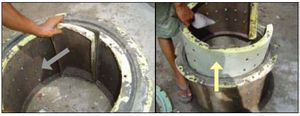
- Remove the nuts in outer mould and separate it carefully from the ring (Plate – 21).
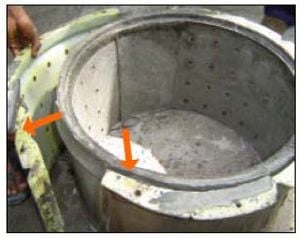
- The plugs that were used for aeration holes need to be removed in 3-4 hours. It is a little bit difficult to remove them after hardening.
- Other components of the bins are easy to separate. A little knocking may be required to loosen the concrete blocks from the moulds.
- These blocks are suitable to use after two weeks of maturating. (It is better to spray some water during the curing period.)
F) Painting
Painting can be done after the initial maturation period (2 weeks). Any colour can be used but dark colours are preferable to absorb more heat from the environment. Green is commonly used due to its association with environmentally friendliness.
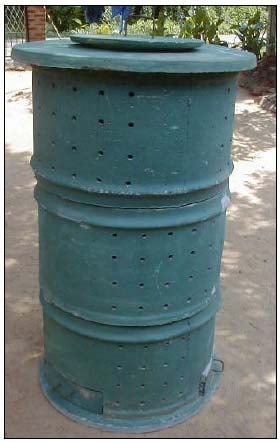
Concrete compost bin manufacturers and mould producers[edit | edit source]
Bin Manufacturers:
Lakna Concrete Works No.125, Hiripitiya, Pannipitiya Tele: 011-4305792/ 071-4058045 Reg. No. WF 4104
Ruhunu Concrete Works K.K.D.Koratuwa Rd Polhena Tel:0412229262/077457133
M.G. Saman Ravindra No.171, Bandaranayakapura Malkaduwawa Kurunegala.
P.M. Prematilaka Silva No.2/234 "Senani" Thuduwa, Hungama
Bin Mould Producers[edit | edit source]
Lakna fibre works No.125, Hiripitiya, Pannipitiya Tel: 011-4305792/ 071-4058045
Prasantha Kumara Mel "Melsiri" Ullala Kamburupitiya Tel: 0773285516
Who to contact[edit | edit source]
Project Manager – Solid Waste Management or the Resource Desk at
Practical Action South Asia
No 5, Lionel Edirisinghe Mw, Colombo 5, Sri Lanka
Tel: +94 (11) 2829412 Fax: +94 (11) 2856188
E-mail: general@practicalaction.lk Web: www.practicalaction.org
For specific training details please contact the Project Officer at Practical Action:
Hambantota (Tel: 047- 4379339 E-mail: southern.staff@itdg.slt.lk)
Ampara (Tel: 063-2224932 E-mail: eastern.staff@itdg.slt.lk)