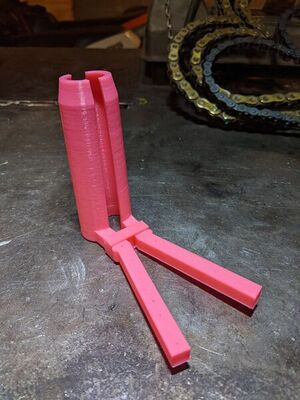
3D printed parts are able to be rapidly produced at low cost making them ideal for disposable medical equipment. In areas where advanced medical equipment or lack of space for sanitizing existing equipment the 3D printer is the next best option. The speculum designed can be used for several different applications in the human anatomy all based on the scale and infill printed at. This speculum takes a different design that current production models to eliminate the need for pivot hardware or large joints. The open jaw design allows for greater operating and inspection area.
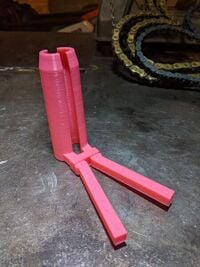
Bill of Materials[edit | edit source]
- PLA plastic- $0.40
- Electricity- $0.25
- Total cost- $0.65 depending on size
Tools needed[edit | edit source]
- MOST Delta RepRap or similar RepRap 3-D printer
Skills and knowledge needed[edit | edit source]
- Basic assembly skills required. All slip fit joints.
Technical Specifications and Assembly Instructions[edit | edit source]
- Print time estimate of 4 hours
- Assembly time estimate of 1 minute
- Print all 4 parts pictured below
- Slide square connector onto bottom of both LH and RH legs
- Slide square connector up to the base of LH and RH cylindrical base
- Insert pivot cylinder into rounded inside edges shown
- Slide square connector between ridges over center of pivot cylinder as shown
- Completed assembly
Common Problems and Solutions[edit | edit source]
- Tolerance on printer is important as parts are slip fit
Cost savings[edit | edit source]
- 75% cost savings compared to $2.66
Benefited Internet Communities[edit | edit source]
BMJ Open source medical harware Openrms Opensource Health Awesome Healthcare GIThub
References[edit | edit source]
.